Navigating the world of industrial materials, swage locked grating emerges as a key player, known for its exceptional durability and robustness. But what makes it a standout choice for different applications? Drawing on extensive expertise and experience, this piece delves into the essential features, benefits, and ideal applications of swage locked grating.
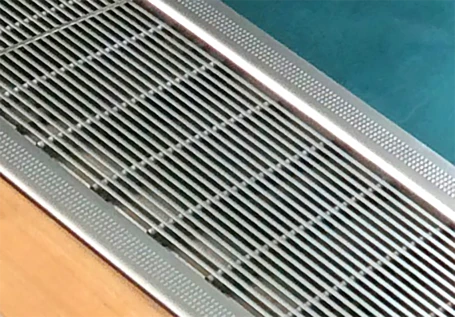
Swage locked grating is crafted through a rigorous process where intense hydraulic pressure is applied, locking the cross bars to the bearing bars using a swaging technique. This method ensures precise alignment and a secure fit, yielding a grating that is both resilient and capable of bearing significant loads without compromise. Known for their impressive strength-to-weight ratio, these gratings are designed to withstand demanding environments, making them indispensable in various industries.
Industries such as oil and gas, petrochemical, and manufacturing often rely on swage locked grating due to its non-slip surface, which is critical for ensuring safety in workplaces where oil, chemicals or moisture could create hazardous conditions. Furthermore, the material's corrosion resistance adds to its longevity, minimizing maintenance costs and downtime—an essential factor for facilities that prioritize operational efficiency and long-term cost savings.
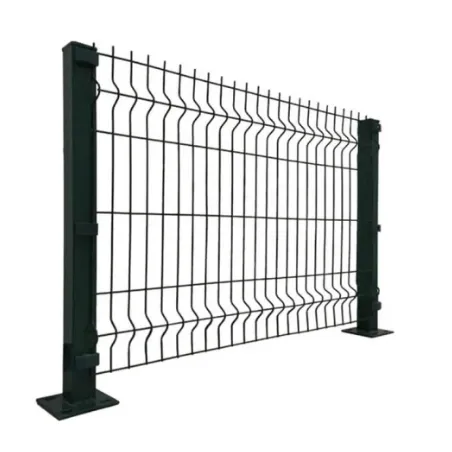
In-depth expertise reveals that one of the standout advantages of swage locked grating is its versatility. Whether used for flooring, mezzanines, walkways, or stair treads, its ability to support substantial weight while allowing for good ventilation and light penetration is unparalleled. This feature is particularly beneficial in industrial and construction settings, where airflow is essential, and visibility beneath the floor surface can aid in inspections and maintenance operations.
swage locked grating
Moreover, the authority of swage locked grating in the industry is further solidified by its adaptability in terms of material choice. Commonly available in steel, aluminum, and stainless steel variations, each offers unique benefits.
Steel grating stands out for its load-bearing capacity and affordability. In contrast, aluminum options are prized for their lightweight nature and corrosion resistance. Stainless steel variations, meanwhile, offer superior durability and resistance to both chemical exposure and environmental factors, making them suitable for specialized and high-demand environments.
Building trust in swage locked grating also stems from its compliance with rigorous safety standards, which vary across geographies but universally emphasize worker safety and environmental considerations. Manufacturers with a commitment to quality ensure their products not only meet but often exceed these standards, providing peace of mind to businesses focused on operational safety and environmental impact.
Drawing from extensive experience in material selection and application, investing in swage locked grating is seen not just as a choice for immediate utility but as a strategic decision that aligns with both present and future needs. It's a testament to how specialized industrial materials continue to evolve, meeting the ever-growing demands for safety, efficiency, and sustainability.
Approaching swage locked grating with this level of understanding and appreciation for its capabilities ensures not only an immediate return on investment but also secures its place as a pivotal tool in modern industry infrastructure. As industries continue to progress, swage locked grating will remain at the forefront, a testament to its indispensable role in creating safe and efficient workplaces.