Serrated gratings are essential components in varying industries, from construction to industrial applications. Their design not only serves a functional purpose, but when crafted with precision, they provide enhanced safety, durability, and efficiency. This article delves into the dimensions of serrated gratings, offering insights into why they are indispensable and how proper dimensioning can optimize their use.
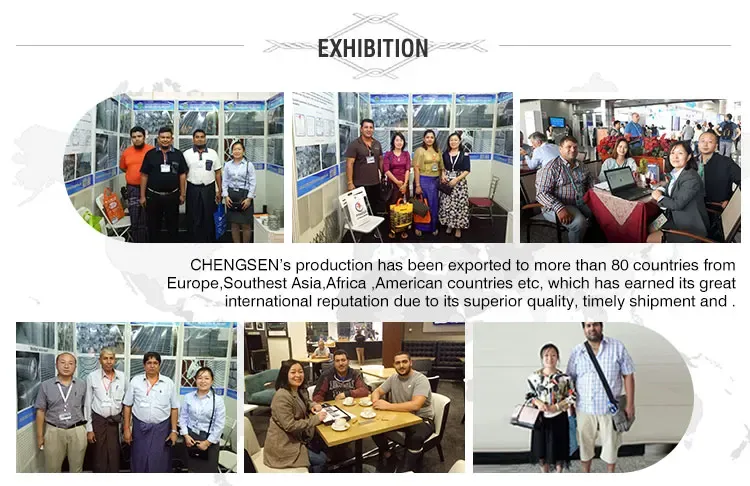
Serrated grating is characterized by its distinctive saw-tooth edges, which provide superior slip resistance—a crucial feature in environments where safety is paramount. The dimensions of these gratings often determine their effectiveness. Standard serrated gratings usually come in panel sizes; for instance, 1x3, 2x4, and other varying dimensions tailored to specific needs. However, the thickness of the bars and spacing also plays a vital role, affecting both the load-bearing capacity and the level of traction provided.
From a specialist's perspective, selecting the optimal dimensions begins with understanding the intended application. In environments where heavy machinery and frequent foot traffic are present, thicker gratings with closer serrated edges are recommended. This dimensioning not only supports increased loads but also ensures the longevity of the grating, thereby delivering cost efficiency over time. For example, a grating with a thickness of 5mm and spacing of 30mm might be ideal for industrial platforms, providing both strength and safety.
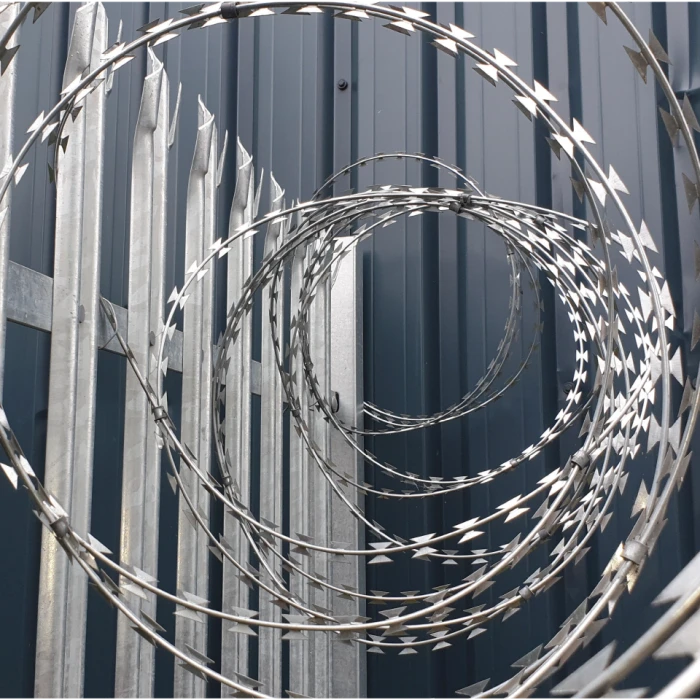
Precision in the dimensions can enhance not just the safety but also the installation process. Correctly dimensioned gratings fit seamlessly into their designated locations, minimizing the need for custom alterations that can incur additional costs. Moreover, precise dimensioning supports easier maintenance as each piece can be removed and replaced with minimal disruption to operations.
serrated grating dimensions
An expert understands that the material of serrated gratings—whether steel, aluminum, or fiberglass—interacts differently with various dimensions. Steel gratings, known for their strength, might suit larger spans and require less frequent supports, while aluminum’s lightweight nature facilitates easier handling, albeit potentially needing more reinforcement. Fiberglass, on the other hand, balances weight and corrosion resistance, suitable for chemical plants, but requires precise dimensional planning to maximize its properties.
The choice of serrated grating dimensions also ties into regulatory compliance, a factor often guided by authorities to ensure workplace safety. Experts stay abreast of standards such as the Occupational Safety and Health Administration (OSHA) and the European EN 14122, which offer guidelines on the permittable dimensions and load specifications of serrated gratings used for walking and working surfaces. Aligning with these standards not only enhances trustworthiness but also underscores commitment to safety and quality, two pillars in any industry.
Over the years, empirical data and use-case studies have shown that tailoring serrated grating dimensions according to specific applications reduces the risk of workplace accidents significantly. Companies investing in professional dimensioning consultations typically report fewer slip-related incidents and reduced costs associated with accidents. This investment pays dividends by fostering a safer work environment, which inherently boosts productivity.
In conclusion,
the dimensions of serrated gratings are not just mere numbers. They are a defining element that influences safety, efficiency, and durability. As industries continue to evolve, the demand for precise, regulated, and expertly designed serrated gratings will only grow. For businesses and professionals dedicated to upholding the highest standards, understanding and implementing the correct dimensions of serrated gratings is paramount. Such expertise not only helps in the efficient deployment of resources but also, more importantly, ensures the well-being of those who rely on these structures every day.