Serrated bar grating dimensions are crucial for various industrial and commercial applications, providing both safety and durability. With decades of experience in the field, it's clear that choosing the right serrated bar grating involves understanding not just the technical specifications but also the real-world application needs.
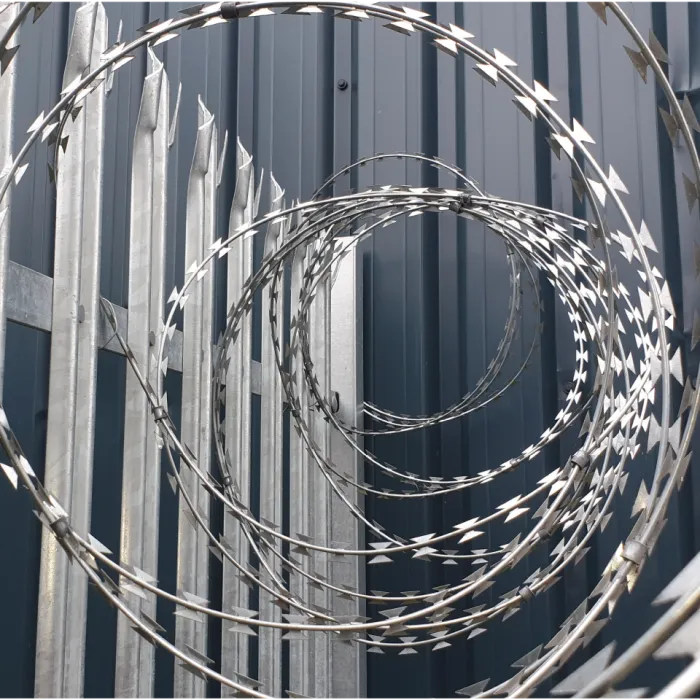
Serrated bar grating is renowned for its slip-resistant surface, a critical feature when it comes to ensuring safety in areas prone to wet or oily conditions. The serrations, typically notched into the bar grating’s surface, are an engineering marvel that enhances traction, reducing the risk of slips and falls. But there's more to it than just safety; the dimensions of these gratings play a pivotal role in their performance.
When considering serrated bar grating dimensions, the focus should be on three key aspects the height of the bars, the spacing between them, and the thickness of the material. Standard bar heights generally range from 1 inch to 2 inches, though custom sizes are also available for specific needs. The height of the bar impacts the load-bearing capacity—taller bars can handle more weight, an essential factor in industrial settings where heavy machinery may be involved.
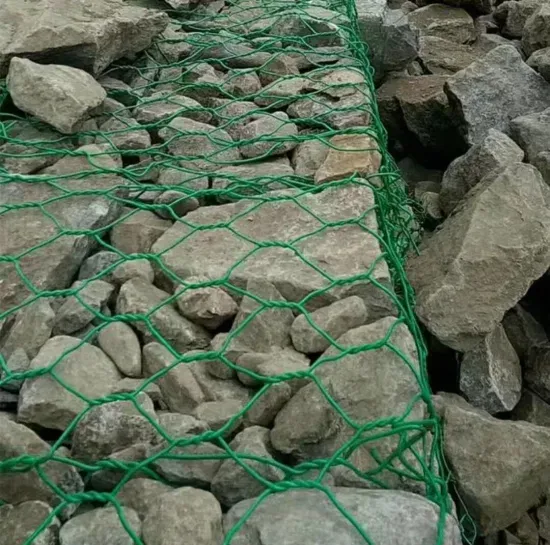
Bar spacing, which is the distance between the centers of two adjacent bars, is typically set at 19/16 inches (1-3/16) or 15/16 inches for heavy-duty applications. This spacing is not a mere aesthetic choice but a strategic one. Wider spacing can handle increased load without compromising structural integrity, while closer spacing offers enhanced support and is better suited for pedestrian traffic, ensuring a comfortable and safe experience for workers.
A crucial but often overlooked aspect of serrated bar grating dimensions is the thickness of the material used. Thicknesses commonly range from 3/16 inch to 1/4 inch. Thicker materials typically offer greater durability and are better suited for high-impact areas. The choice of material thickness should align with the expected traffic and load requirements—industries such as mining or heavy manufacturing may require the sturdiest options available.
serrated bar grating dimensions
Over the years, many safety managers and engineers have shared their experiences with serrated bar grating, highlighting its versatility. For example, in a case study involving a manufacturing plant, the choice of a bar height of 1-1/2 inches combined with a 15/16-inch spacing and 1/4-inch thickness proved to be optimal. This configuration not only supported the heavy machinery moving about the plant floor but also ensured that workers had adequate traction, thereby minimizing workplace accidents.
The expertise required to select the appropriate serrated bar grating extends beyond mere dimensions. One must consider the environmental conditions, such as exposure to chemicals or temperature extremes, to choose the right material—typically steel, aluminum, or stainless steel. Each material offers different advantages; for instance, stainless steel provides superior corrosion resistance, making it ideal for outdoor or corrosive environments.
Furthermore, a trustworthy supplier will often allow for custom configurations, tailoring the grating dimensions to the client’s specific needs. This customizability is a testament to the flexibility of serrated bar gratings in meeting diverse industrial requirements. It also ensures long-term cost-effectiveness, as companies invest in grating that precisely matches their operational demands without unnecessary overspend.
Ultimately, the choice of serrated bar grating dimensions should be guided by a combination of technical specifications and practical insights from those who have worked with the material in real-world settings. Collaboration with experienced engineers and reputable suppliers is essential, ensuring an authoritative approach that balances safety, efficiency, and longevity.
Benchmark studies and field reports consistently affirm the efficacy of well-chosen serrated bar gratings, highlighting their indispensability in industrial safety solutions. These gratings not only meet but often exceed expectations, cementing their reputation as a vital component in modern industrial infrastructure.