Gratings, an integral component in a multitude of industrial and commercial applications, are often overlooked yet play a crucial role in ensuring safety and functionality. From defining pathways in warehouses to providing drainage solutions in urban architecture, the right grating can make a significant difference in both performance and safety. This article delves into the multifaceted world of gratings, drawing from years of industry expertise to provide insights that underscore their importance and utility.
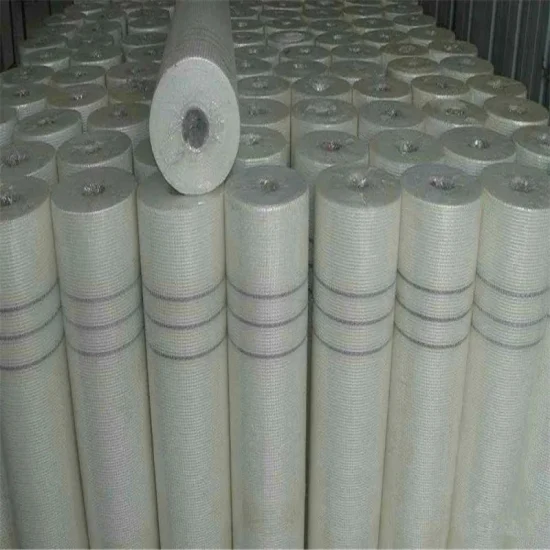
Gratings are typically fabricated from materials like steel, aluminum, or fiberglass, each chosen for its specific benefits. Steel gratings are renowned for their strength and durability, making them ideal for heavy-load environments such as shipping docks and construction sites. The inherent rust resistance of stainless steel gratings also makes them suitable for corrosive environments, such as chemical plants. On the other hand, aluminum gratings, due to their lightweight nature, are perfect for situations where ease of handling and installation is paramount without compromising on strength. Meanwhile, fiberglass gratings offer unmatched resistance to chemicals and are perfect for industries like marine and chemical processing where metal gratings would quickly degrade.
The design of gratings also influences their application. Bar gratings, with their linear pattern, provide excellent load-bearing properties and are often used in industrial floors and walkways. Conversely, molded gratings, typically made from fiberglass, offer anti-slip surfaces perfect for wet environments, reducing workplace accidents. Recent innovations have also seen the introduction of decorative gratings for architectural purposes, merging function with aesthetics to enhance public spaces.
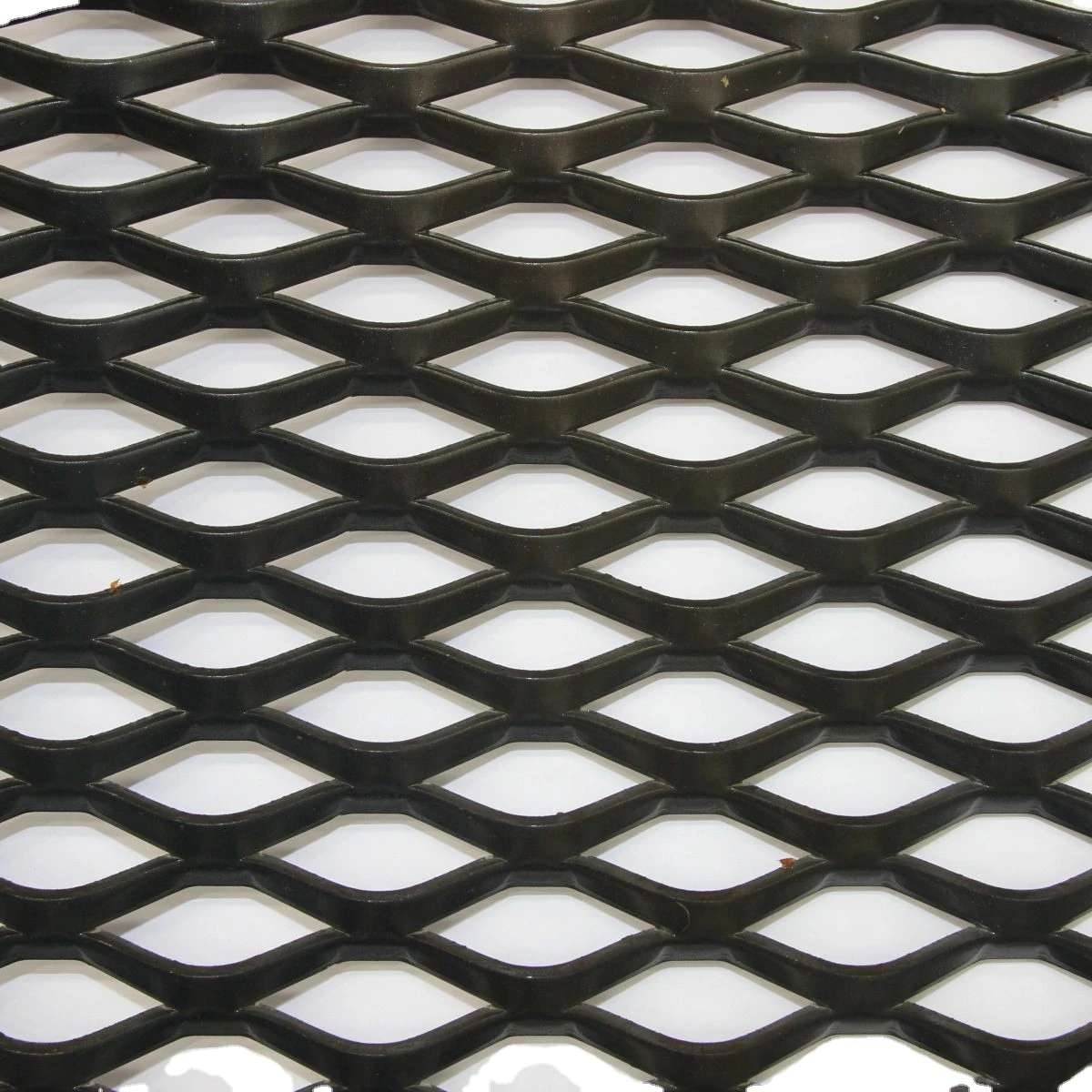
From an experiential standpoint, choosing the right grating involves understanding the environment in which it will be used. For instance, a facility manager from a chemical plant shared their experience of transitioning from steel to fiberglass gratings in key areas, resulting in improved longevity and safety due to the non-corrosive properties of fiberglass. Such real-world applications highlight the need for meticulous planning and expert consultation when selecting gratings.
gratings
Expertise in gratings not only requires understanding their material and design but also the standards governing their use. Gratings must comply with safety and quality standards like the ASTM and ANSI, ensuring they are fit for purpose. Adhering to these standards not only guarantees safety but also instills confidence in clients about the reliability of the gratings employed.
Authoritative knowledge in this domain extends beyond materials and standards to encompass installation practices. Proper installation is critical to the performance of gratings, as misaligned or improperly secured gratings can lead to accidents or structural failures. Training and certification programs are available for professionals involved in the installation of gratings, emphasizing best practices and safety guidelines.
Trustworthiness in the context of gratings is built on consistent product performance and adherence to safety standards. Working with reputable manufacturers and suppliers ensures that the gratings installed are of high quality and provide the intended benefits. Supplier audits, material testing, and feedback from end-users contribute to a continuous improvement cycle that enhances the trust factor associated with grating products.
In conclusion, gratings are more than just functional components; they are essential to the safety and efficiency of the environments in which they are used. Through a deep understanding of their materials, applications, and installation, alongside compliance with safety standards, one can leverage gratings to their fullest potential. Whether it's providing safe access in an industrial setting or enhancing the aesthetic appeal of a public space, gratings are indispensable tools in modern infrastructure and design.