Finding the right bar grating for your project can be a challenging task given the diverse options available in the market. Yet, comprehending the nuances and distinguishing features of each type can make the decision-making process much smoother. In my years of working extensively within sectors that frequently use bar grating, such as construction, infrastructure development, and industrial manufacturing, I've gained a wealth of insights to share.
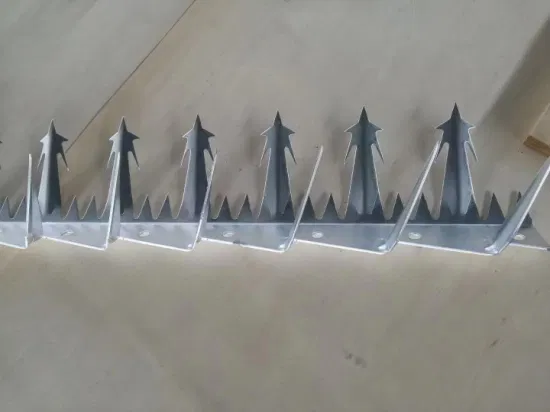
Bar grating is more than just a structural component; it's a pivotal element in ensuring safety, durability, and efficiency in various applications. Professionals across industries trust it due to its strength, versatility, and cost-effectiveness. Notably, the selection of material and type of bar grating can greatly influence its effectiveness in a particular setting.
One of the primary materials for bar grating is steel, known for its robustness and wear resistance. When galvanized, steel grating offers enhanced resistance to corrosion, making it ideal for environments exposed to elements like rain and chemicals. However, in settings where preventable rusting is less of a concern, plain steel is often preferred for its cost efficiency. A lesser-known but equally efficient material is aluminum, prized for its lightweight properties without compromising on strength. For projects requiring non-sparking, corrosion-resistant components, fiberglass grating is the optimal choice, aligning perfectly with environments where electrical conductivity must be minimized.
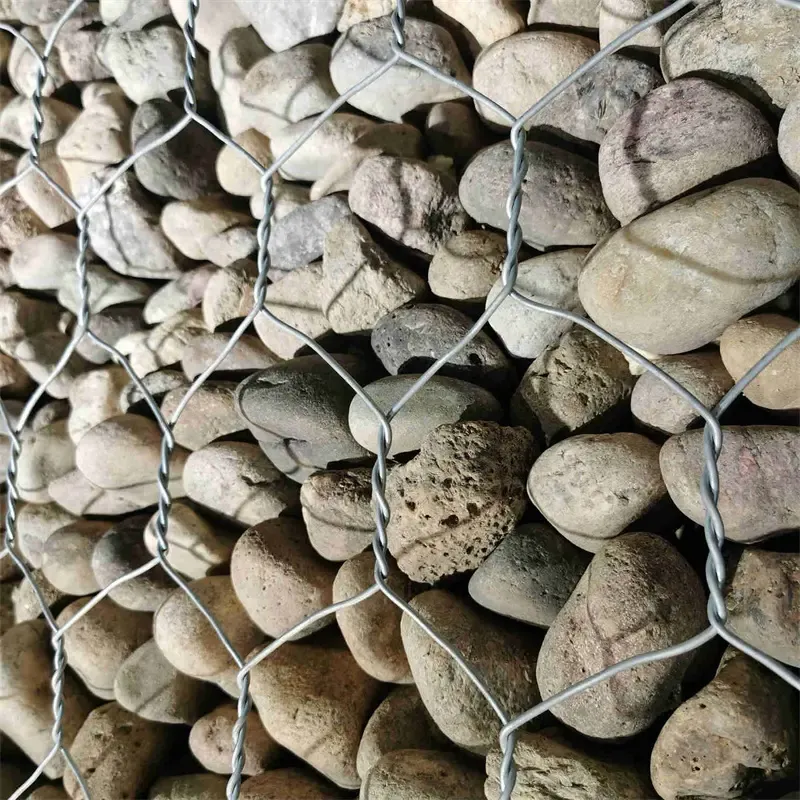
Bar grating isn't just about material choice; its configuration plays an equally crucial role. Welded bar grating, for instance, is a staple in load-bearing applications due to its high strength-to-weight ratio. Press-locked bar grating, on the other hand, is noted for its aesthetic appeal and is often utilized in architectural designs where the visual element is as significant as functionality. Meanwhile, swaged and riveted grating types cater to specific needs such as lighter loads or additional flexibility in placement.
bar grating
Installing bar grating demands comprehensive knowledge to ensure its long-term performance and safety. Proper installation hinges on considering factors such as anticipated load levels, potential environmental stressors, and alignment precision. Missteps during installation can compromise both the structural integrity and intended functionality of the grating. Therefore, relying on experienced professionals for installation is advisable, ensuring that industry standards and best practices are adhered to.
From a maintenance standpoint, while bar grating is inherently low maintenance, routine inspections are indispensable to identify signs of wear or potential safety hazards. Especially in high-traffic or industrial environments, regular checks can preempt costly repairs or replacements by addressing minor issues before they escalate.
Bar grating continues to be an essential asset across myriad sectors, and understanding its multifaceted nature ensures that it fulfills its intended role efficiently. Trusted industry experiences, coupled with expert insights, not only aid in making informed purchase decisions but also instill confidence that your choice of bar grating will deliver sustained performance. As the landscape of industrial and construction materials evolves, staying informed and updated on the latest advancements in bar grating technology remains a priority for industry experts, ensuring that every project not only meets but exceeds expectations.