Understanding the pricing dynamics of grating plates is crucial for businesses and individuals planning projects that require durable and efficient flooring solutions. Grating plates, often utilized in industrial, commercial, and even residential settings, provide a robust option for flooring, walkways, and trenches due to their strength and versatility. This article deciphers the factors influencing grating plate prices, offering insights from industry experts to help guide your purchasing decisions.
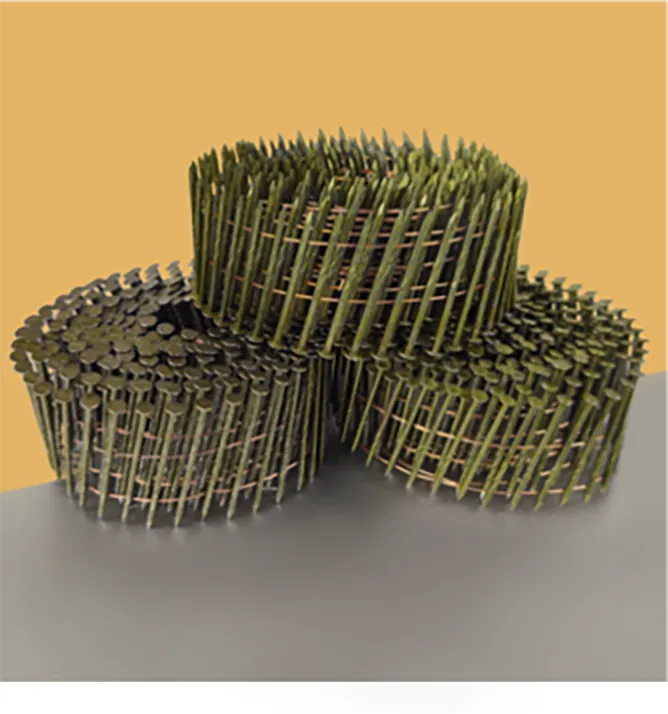
Grating plates are available in a multitude of materials, each contributing differently to the overall cost. Steel, aluminum, and fiberglass are among the most popular choices. Steel grating plates are often the most cost-effective option, providing strength and longevity; however, their price can fluctuate due to market conditions affecting steel supply and demand. Aluminum grating plates, while typically more expensive than steel, are favored for their lightweight yet sturdy properties, making them ideal for installations where weight is a concern. Conversely, fiberglass grating plates offer excellent corrosion resistance, suitable for chemical processing environments, albeit at a higher price point due to their specialized manufacturing process.
Expertise suggests that the size and configuration of the grating plate are significant determinants of price. Standard sizes are generally more economical due to mass production, but custom sizes required for specific projects could elevate costs. Additionally, the grid pattern or mesh size, which can affect load-bearing capacity and visual aesthetics, may also influence pricing. For instance, tighter mesh patterns often require more material and labor, thus increasing the overall expense.
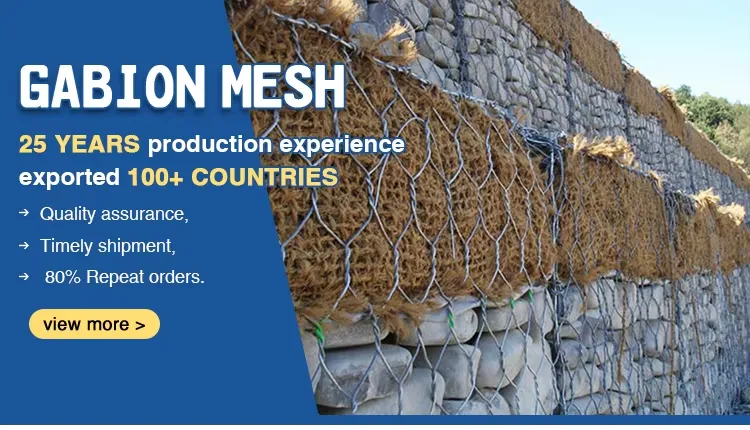
From an authoritative standpoint, it's crucial to consider the load requirements of your application when determining which grating plate to purchase. Typically,
grating plates are categorized into light, medium, and heavy-duty options. Light-duty grating is suitable for pedestrian traffic and lighter loads, making it a less costly option. In contrast, heavy-duty plates, designed to withstand vehicular and heavy machinery traffic, come at a premium due to their enhanced capabilities.
grating plate price
It's also noteworthy that additional features or treatments, such as galvanization, anti-slip coatings, or special finishing, can impact the cost of grating plates. A galvanized finish can extend the life of a grating plate by protecting it against corrosion, particularly in outdoor or moisture-prone environments, justifying the extra expense. Similarly, anti-slip coatings, a safety requirement in many settings, can add to the cost but provide a worthwhile investment in terms of safety and compliance with regulatory standards.
The trustworthiness of supplier sources and the transparency of pricing structures should not be overlooked. Securing a reliable supplier that is transparent about costs, from raw materials to finished products, and offers robust after-sales support, can significantly affect both the purchasing experience and the long-term value you're able to derive from your investment in grating plates.
In conclusion, understanding the myriad of factors influencing grating plate prices involves a careful evaluation of material choice, size and configuration, load requirements, special treatments, and supplier credibility. By doing so, one can make informed decisions that not only meet budgetary constraints but also maintain the integrity and safety of the application for which the grating plates are intended. Investing time in research and consultation with seasoned industry professionals will ensure that the selection of grating plates aligns well with both project specifications and financial considerations.