When exploring the versatile world of construction materials, grating galvanized steel emerges as a standout choice for many industrial applications. This material offers a blend of strength, durability, and resistance to corrosion, making it invaluable in environments that require robust solutions.
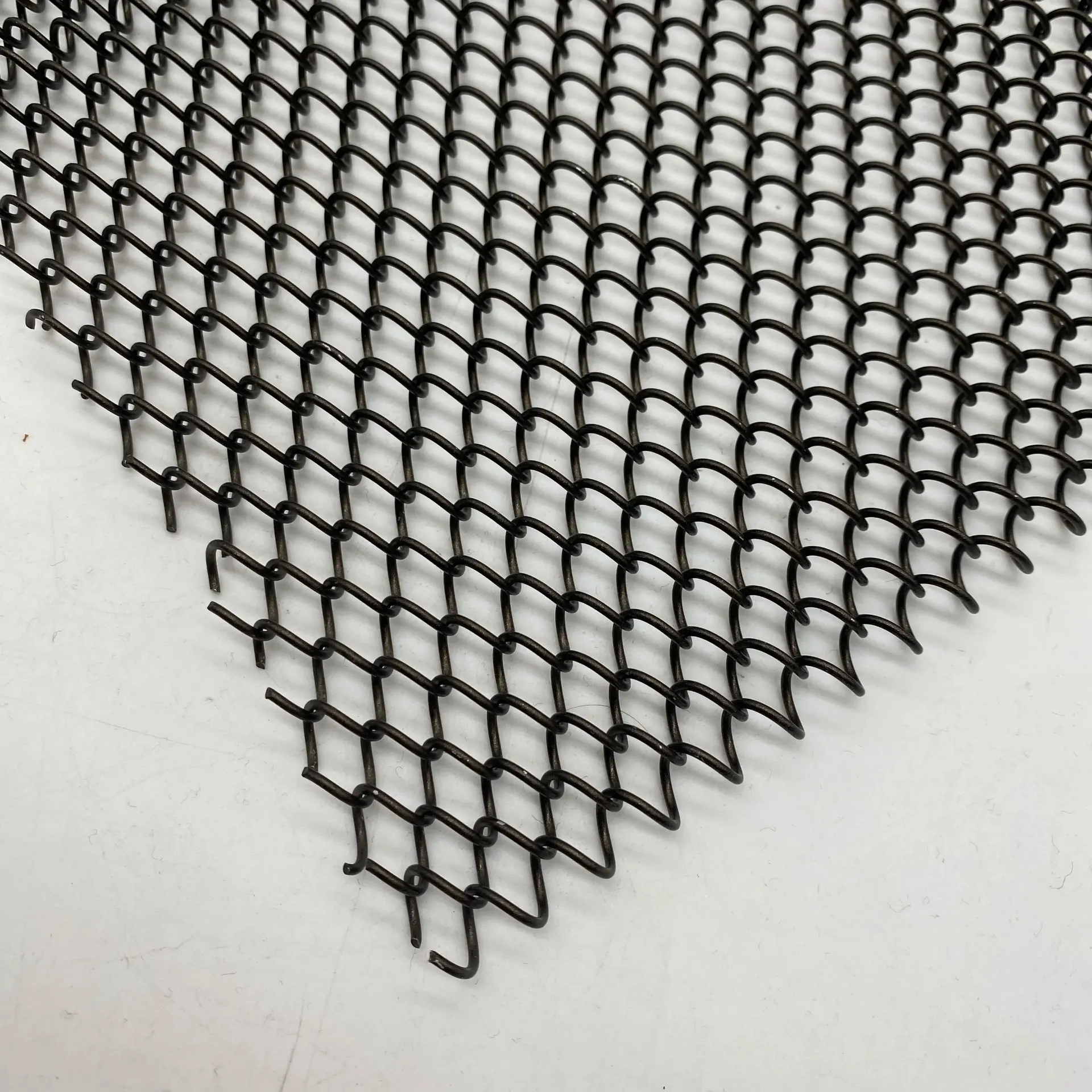
In high-demand industrial settings, grating galvanized steel demonstrates remarkable resilience. Its manufacturing process involves the immersion of steel in molten zinc, serving as a corrosion-resistant coating that significantly enhances the life span of standard steel. This galvanization process creates a defense barrier against environmental factors like humidity and pollutants, making it ideal for both indoor and outdoor use.
Furthermore, those who have extensively worked with grating galvanized steel appreciate its exemplary performance in terms of load-bearing capacity.
Unlike traditional steel, the galvanized variant ensures fewer maintenance needs over time. This material is notably well-suited for use in flooring systems, walkways, and platforms in factories and power plants, reducing the frequency of repairs and replacements.
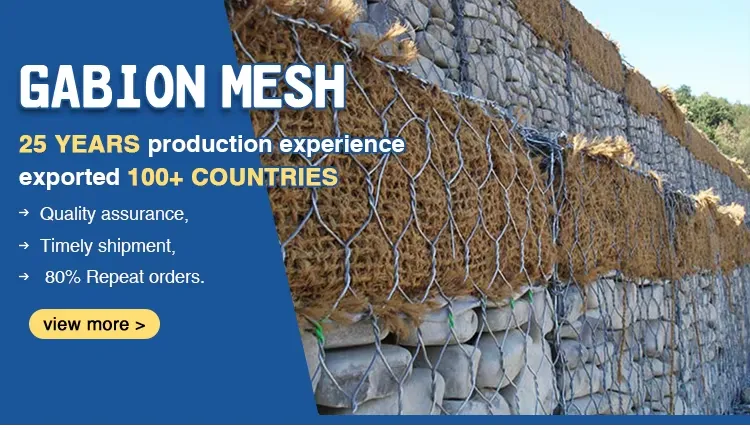
From an expertise standpoint, the adaptability of grating galvanized steel is unmatched. The steel can be configured into various designs and specifications, tailored to meet specific project requirements. For instance, heavy-duty grating can be employed in areas subjected to extreme conditions or substantial weight loads, while lighter variants might suffice for pedestrian walkways. This versatility underscores its utilization across diverse sectors, from civil engineering to infrastructure development.
An authoritative aspect of grating galvanized steel comes from its compliance with rigorous safety norms and standards. Many high-profile industrial projects rely on galvanized steel gratings that meet specifications such as those set by the American Society for Testing and Materials (ASTM). Compliance ensures heightening safety measures that protect environments from structural failures, thus safeguarding human life and property.
grating galvanized steel
Real-world applications of grating galvanized steel reveal substantial gains in operational efficiency. Industries often narrate experiences highlighting considerable cost savings over long-term use. This is attributed to the material's lower depreciation compared to non-galvanized counterparts, resulting from its outstanding resistance to rust and corrosion. This factor alone results in enhanced trustworthiness among project managers and site engineers, who often witness first-hand the material's reliability.
Moreover, incorporating grating galvanized steel in development projects aligns with sustainable construction practices. The longevity and recyclability of galvanized steel contribute to sustainable development goals, reducing environmental impact and supporting eco-friendly initiatives. Its ability to withstand harsh climatic conditions without succumbing to degradation further supports environmental conservation efforts.
The implementation process is streamlined by knowledge-sharing across the construction industry landscape. Insights from seasoned professionals reveal that installation is straightforward, often requiring minimal specialized equipment. Experienced engineers and builders often emphasize on pre-planning and appropriate load assessments to maximize installation effectiveness. Such insights are valuable, ensuring that the broader community makes informed decisions when employing grating galvanized steel in projects.
In summary, grating galvanized steel positions itself as a material of choice among experts for its durability, adaptability, and compliance with safety standards. Its role in cost management, environmental sustainability, and ease of implementation further establishes its value in construction and industrial environments. The collective experiences and expertise associated with this material enhance its credibility, consistently earning trust through proven performance across applications.