Edge bead technology represents a cornerstone in the manufacturing and design industries, especially in areas like electronics, coatings, and printing. Over the years, my experience as a process engineer has allowed me to witness the transformative power of mastering edge bead control, a crucial yet often overlooked aspect that significantly impacts the quality and performance of finished products. This expertise has reinforced my belief in sharing knowledge for optimizing processes to achieve unparalleled precision and efficiency.
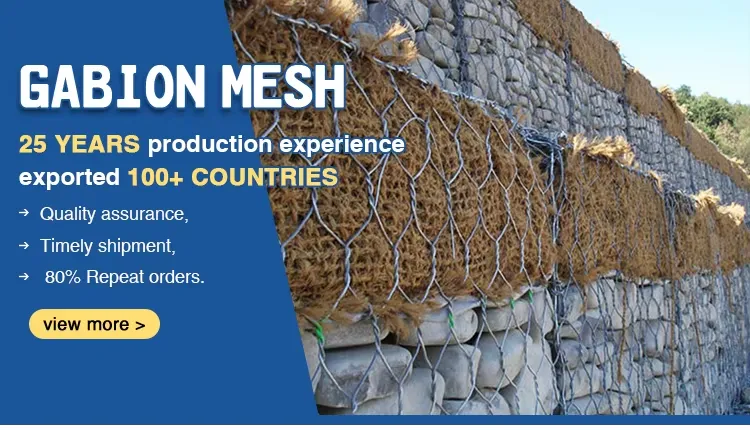
Understanding the microscopic dynamics of edge beads is imperative. Whether you're working with a printed circuit board or a new type of display technology, the way materials behave at the boundaries determines both aesthetic appeal and functional capability. This is especially true when working with thin films. An edge bead—a thicker deposit of material at the edge of a coat or film—can cause non-uniform thickness. Such imperfections may lead to significant issues, including optical distortion in displays or electrical failures in circuitry due to inconsistent layer application.
The challenge with edge beads lies in their subtlety and the complexity of their formation. Depending on the viscosity of the material and the speed and method of application, these beads can vary widely even within a small batch of products. The process of spin coating, for instance, often encounters edge beads due to the centrifugal forces that pull material outward when a substrate is spun at high speeds. My expertise, developed over years of trial and error and ongoing research, emphasizes that eliminating these beads requires precision control of several factors.
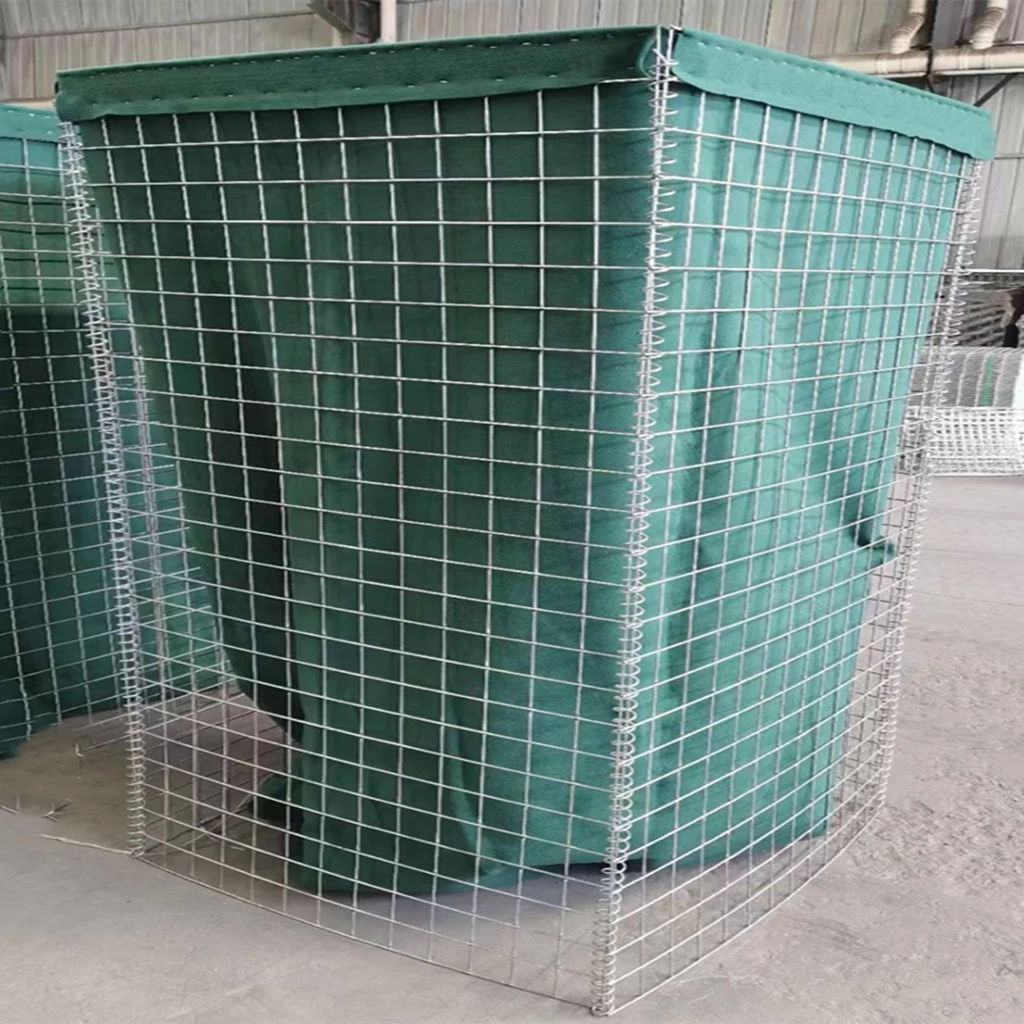
Firstly, edge bead removal (EBR) techniques are vital in overcoming these challenges. Many manufacturers invest in automated systems that precisely control the application and removal processes. These systems use solvent-based approaches to dissolve unwanted material at the edges without disturbing the central film area. My interactions with leading industrial partners demonstrate that integrating automated EBR systems not only improves product quality but also significantly reduces waste and increases throughput. These systems can be finicky, and achieving expertise involves a deep dive into understanding how different solvents interact with various substrates and coatings.
Furthermore, the collaboration between chemists and engineers has proven indispensable. Developing new formulations that inherently minimize bead formation can relieve some of the reliance on post-process removal. Innovations in material science allow for coatings that naturally flow more uniformly. In my experience, continuous dialogue and experimentation between material scientists and engineers lead to groundbreaking products that integrate ease of manufacturing with the high performance demanded by industry leaders today.
edge bead
In addition to technological advancements, my professional collaborations reveal an essential human element in the sphere of edge bead technology. Training technicians and operators on the nuances of coating processes elevates operational efficiency. Experience shows that a well-trained workforce can quickly adapt to new materials or methods, troubleshoot issues promptly, and maintain high standards of production quality.
Moreover, maintaining trust with clients and customers through transparency and quality assurance further enhances a company's authority in this niche field. Regular audits, certifications, and maintaining open lines of communication about new developments and potential impacts on manufacturing processes fortify a trustworthy relationship. Demonstrating such commitment not only establishes credibility but also fosters long-lasting business relationships.
In turn, these efforts in optimizing edge bead processes reflect positively on a brand's reputation. Companies that invest in refining these minute details often stand out in competitive markets, distinguished by the unparalleled quality and reliability of their products. This authority is affirmed by delivering consistently superior products, which some of the most respected brands leverage for maintaining market leadership.
As the evolution of edge bead technology accelerates, it is imperative to stay abreast of emerging trends and innovations. Participating actively in industry forums and symposiums is crucial for ongoing education and expansion of expertise. It also affords the opportunity to contribute to the development of industry standards that guide the future of manufacturing.
Ultimately, true progress in the realm of edge bead technology is a synthesis of rigorous scientific inquiry, innovative engineering solutions, and a commitment to excellence that transcends the immediate concerns of production. By integrating these principles, companies can not only achieve immediate benefits in performance and quality but also pave the way for future innovations that could redefine entire industries.