Navigating the cost of steel grating involves understanding a range of factors that impact its market price, quality, and suitability for different applications. By focusing on experience, expertise, authoritativeness, and trustworthiness, this guide aims to illuminate the key considerations and best practices in purchasing steel grating.
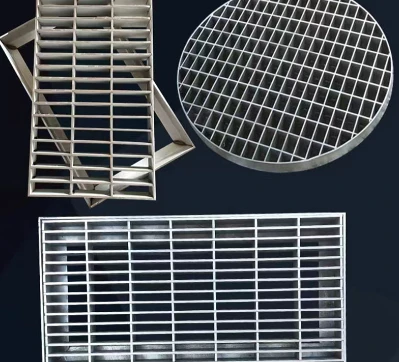
Steel grating is essential in industrial and commercial projects, providing robust support and safety features across various applications such as walkways, stair treads, and flooring. One of the initial considerations when assessing the cost of steel grating is the type of material used. Steel grating can be manufactured from a variety of materials, including carbon steel, stainless steel, and aluminum, each offering different benefits in terms of strength, corrosion resistance, and weight. Carbon steel is generally the most economical choice with reasonable strength, while stainless steel provides superior resistance to corrosion, serving well in harsh environments though at a higher cost. Understanding the specific requirements and constraints of your project can lead to more cost-effective decisions.
The manufacturing process also impacts the overall cost. Steel grating can be either press-locked or welded. Welded grating typically shows greater strength and durability due to its construction, where steel bars are welded at their intersections. This method is ideal for heavy-load applications. In contrast, press-locked grating is more precise and aesthetically pleasing, which might be more appropriate for lighter applications or architectural projects. Depending on your budget and requirement for strength or visual appearance, choosing the right manufacturing method can influence the cost-effectiveness of your purchase.
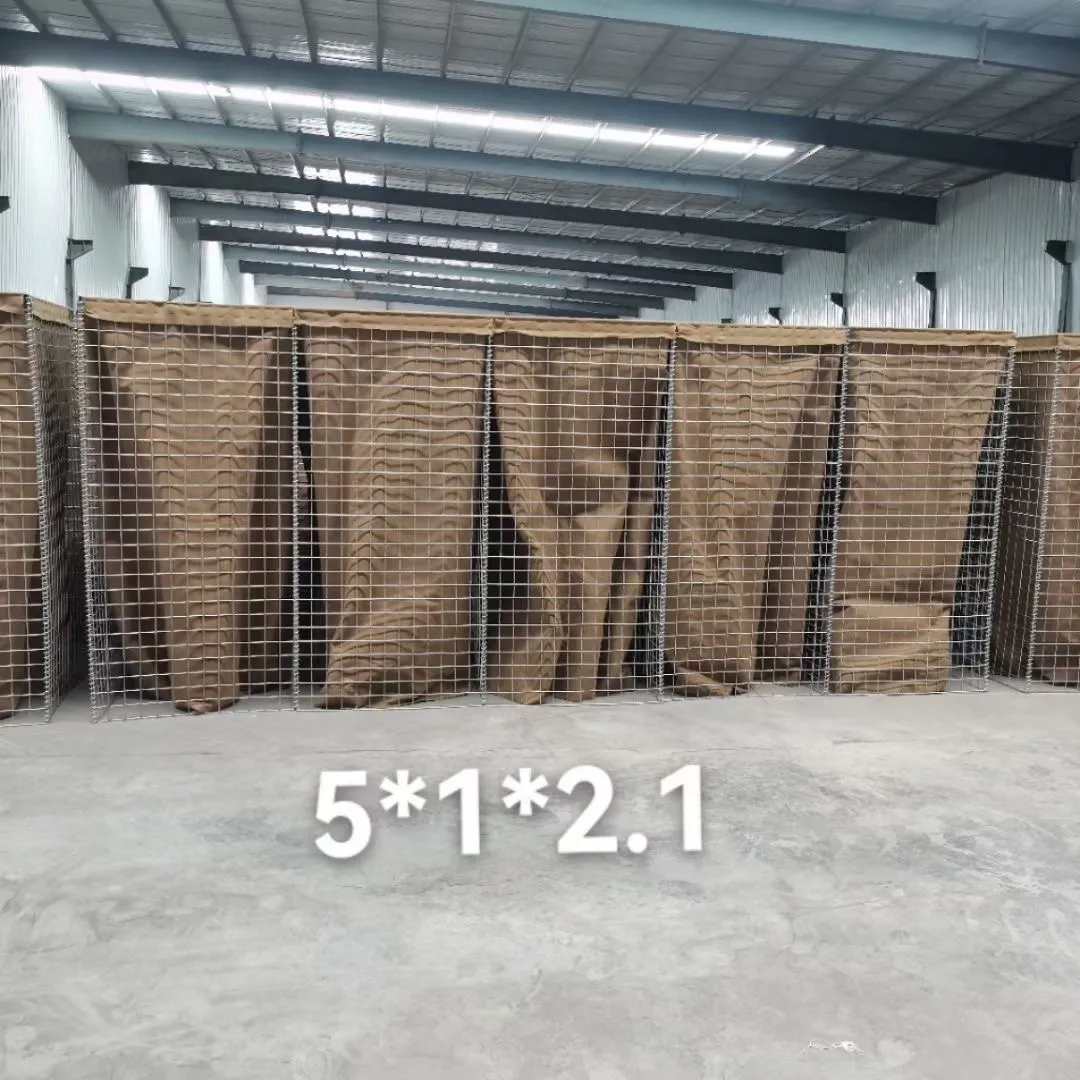
Another element to consider is the size and configuration of the grating. Standard sizes and configurations are generally less expensive as they are produced in bulk, reducing manufacturing costs. However, custom sizes may be necessary for specific applications and can escalate costs due to the additional labor and material wastage involved. Ensuring precise measurements and specifications during the planning stages can help mitigate unnecessary expenses.
Surface treatment is an essential aspect, particularly when considering longevity and maintenance costs. Steel grating is often galvanized or powder-coated to protect against corrosion and wear. Galvanization provides a protective layer of zinc, which is highly effective in preventing rust, a common issue in outdoor or high-moisture environments. Although galvanization may increase initial costs, the investment can lead to significant savings in terms of maintenance and replacement over time. Powder-coating, while sometimes seen as mainly aesthetic, also adds an extra layer of protection and comes in a variety of colors, offering flexibility in matching existing structures.
cost of steel grating
Transportation and installation costs are frequently overlooked but significantly impact the total expense. Steel grating is heavy and bulky, and shipping costs can accumulate quickly, especially for larger orders or if the supplier is located far from the installation site. It’s advisable to collaborate with a supplier who provides competitive shipping rates or local options to minimize these expenses. Additionally, installation should be considered; hiring skilled professionals ensures proper and safe placement, optimizing the grating's lifespan and performance.
Regulatory compliance and quality assurance are critical when purchasing steel grating. Products should adhere to industry standards such as those set by ASTM International or the British Standards Institution. Ensuring compliance not only guards against potential legal issues but also guarantees that the grating will perform to expected safety and reliability standards. When a manufacturer demonstrates adherence to these standards, it strengthens their credibility and bolsters buyer confidence.
Finally, establishing a long-term relationship with a reputable supplier can yield economic benefits. Trustworthy suppliers offer consistent product quality, reliable delivery schedules, and post-purchase support, which can prove invaluable across multiple projects. Seeking suppliers with proven track records and industry certifications affirms their capability and integrity in providing not only competitive pricing but also superior service and support.
In conclusion, the cost of steel grating is influenced by myriad factors, including material type, manufacturing process, size, surface treatment, transportation, installation, and compliance with industry standards. By carefully evaluating these criteria and fostering relationships with trustworthy suppliers, decision-makers can achieve cost-effective solutions without compromising on quality or performance, positioning themselves well in the competitive landscape of industrial and commercial construction.