For anyone involved in construction, agriculture, or industrial project management, understanding wire mesh gauge offers a pathway to selecting the most suitable materials for different applications. Navigating through the myriad of wire mesh options can be daunting without grasping the nuance of its gauge, which is a critical measure of quality and performance. Here's a deep dive into the world of wire mesh gauge and how it impacts decision-making.

Wire mesh gauge essentially refers to the thickness of the wire used in the mesh, a vital component that dictates its strength, flexibility, and overall durability. Typically, a lower gauge number indicates a thicker wire, while a higher number signifies a thinner construction. This counterintuitive numbering system is crucial knowledge when it comes to ensuring the suitability of wire mesh for its intended purpose.
In practical applications, using wire mesh with the correct gauge can significantly affect the integrity and longevity of the project. For example, in construction scenarios where the mesh is intended to support heavy loads or withstand external pressures, a lower gauge (thicker wire) would be the optimal choice. This ensures that the wire is robust enough to handle stress without compromising the safety or stability of the structure.
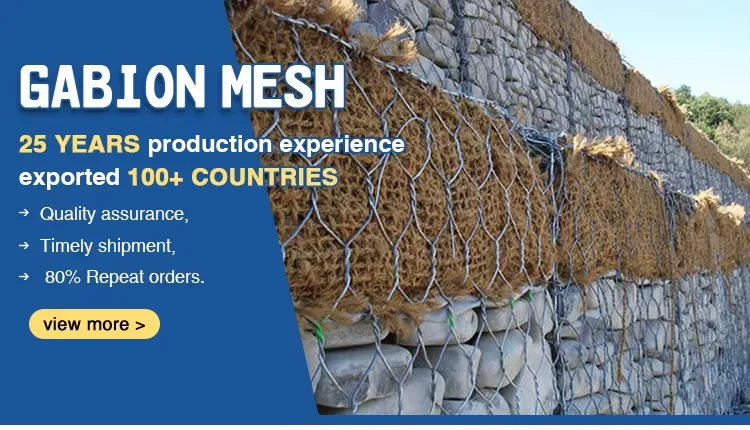
In agricultural settings, where the wire mesh is often used for fencing, a balance needs to be found between strength and flexibility. For fencing livestock, a medium gauge may provide sufficient strength to prevent deformation or breakage without being too rigid or heavy. Additionally, considering the climate and environmental conditions is pivotal; in coastal or highly humid areas, choosing a galvanized wire mesh with an appropriate gauge can help prevent rust and corrosion, thereby extending the mesh’s life.
From an industrial perspective, where wire mesh may be used in filtration or separation processes, the gauge should harmonize with function. Thinner gauges can be advantageous in situations where fine filtration is necessary, allowing for precise and efficient separation. Conversely, in industrial scenarios requiring screens for bulk handling, such as gravel or coal separation, a heavier gauge promises durability and lower risk of damage.
wire mesh gauge
In addition to practical application, the material properties of the wire mesh, influenced by gauge, are significant in specialized areas like aerospace or automotive engineering. Here, precision is paramount, and the gauge must be exact to specifications to ensure compatibility with other components and maintain the high standards these industries demand.
Neglecting to consider the appropriate wire mesh gauge may lead to costly errors. For instance, overestimating the required gauge can result in unnecessary expense without proportionate benefit, while underestimating it can lead to premature wear or catastrophic failure. Therefore, consulting with experts who possess extensive experience and authority in materials engineering can provide critical assurance and invaluable insights in choosing the correct gauge.
Moreover, trustworthiness in wire mesh products can be enhanced by sourcing from reputable manufacturers who comply with industry standards and offer transparent specifications. This due diligence ensures that the wire mesh not only meets the necessary mechanical requirements but also aligns with safety and regulatory obligations specific to the project at hand.
Defining project requirements and understanding wire mesh gauge can also improve cost efficiency. Investment in the right gauge from the onset can prevent additional costs associated with replacements, repairs, or maintenance.
It further averts potential disruptions or downtimes that can arise from compromised mesh performance.
In conclusion, comprehending wire mesh gauge is not just about measuring a product's dimensions. It’s about aligning material science with application needs, ensuring quality through authoritative expert guidance, and maintaining an unwavering commitment to safety and efficiency. As industries from construction to high-tech fields continue to evolve, so too will the applications and demands on wire mesh – making an understanding of its gauge ever more critical for professionals and decision-makers.