When considering construction projects that involve concrete, wire mesh plays a crucial role in enhancing strength and durability. Wire mesh for concrete is not a one-size-fits-all solution. It's designed to cater to specific needs depending on the project's requirements, and the choice of the right type can significantly influence the project’s success. This guide delves into the various types of wire mesh for concrete, providing insights derived from experience, expertise, and authoritative sources to help you make informed decisions.
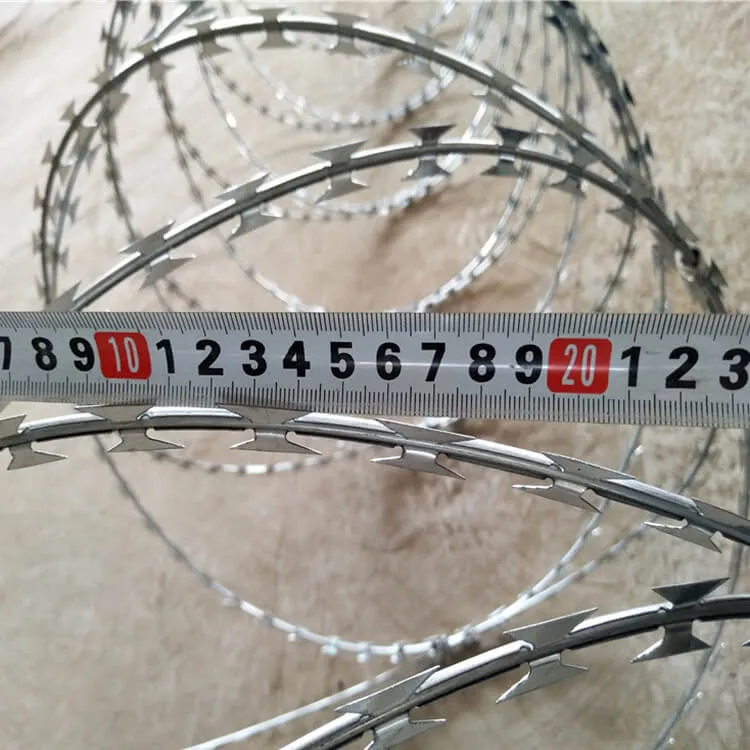
The most common type of wire mesh used in concrete is welded wire mesh. It is made by welding metal wires at intersections to form a grid. Its primary advantage is the enhanced rigidity, which provides excellent reinforcement for horizontal concrete slabs. Because it's prefabricated, it reduces labor costs and accelerates the construction process. Welded wire mesh is ideal for projects like highway pavements and commercial building floors where tensile strength and structural integrity are critical.
For projects requiring shape adaptability, woven wire mesh offers flexibility that welded wire mesh lacks. The intertwining of wires without welding allows this type of mesh to fit irregularly shaped forms, making it suitable for complex architectural designs. This flexibility does not come at the cost of strength; woven wire mesh still offers a significant level of reinforcement, preferred for decorative concrete installations or architectural facades.
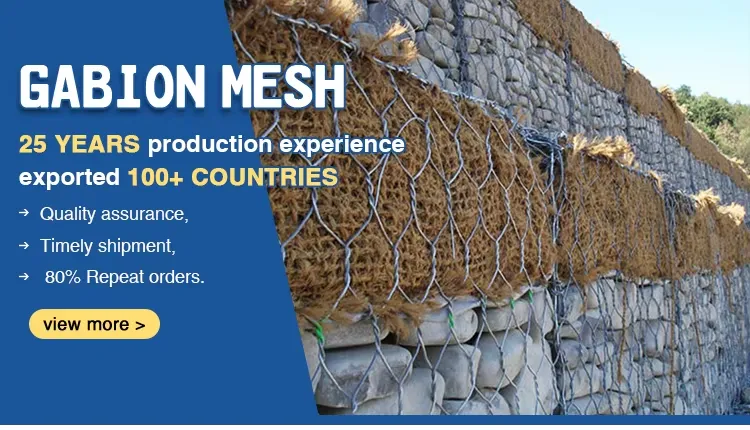
Expanding on specialized needs, the galvanized wire mesh stands out in settings prone to moisture. The galvanization process involves coating the wires with a layer of zinc, providing superior corrosion resistance. This type is particularly beneficial for basement floors and other subterranean concrete applications where moisture exposure is a concern. Moreover, it extends the longevity of the concrete by preventing rust and subsequent weakening of the structure.
Stainless steel wire mesh is synonymous with robustness and is often used in scenarios where maximum durability is required. Its inherent resistance to rust and corrosion makes it perfect for coastal constructions or chemical facilities exposed to harsh environmental conditions. Though its upfront cost is higher, the longevity and minimal maintenance costs often justify the investment, especially in industrial or maritime settings.
types of wire mesh for concrete
Another variant is plastic-coated wire mesh. This type provides an additional protective layer against chemicals and moisture while reducing potential wire visibility for aesthetic purposes. It's increasingly used in residential settings, where the visual impact must be minimized without compromising on structural support.
Consider the use of expanded metal mesh, which offers excellent bonding with concrete because of its diamond-shaped openings. The expanded metal mesh creates a strong mechanical grip, preventing slippage between the mesh and concrete. This property is particularly advantageous in vertical applications such as walls or columns, where maintaining bond strength is critical to the structural integrity.
A lesser-known but increasingly adopted variety is fiberglass wire mesh. It is rust-resistant and very lightweight, reducing the transportation and handling burden. Fiberglass mesh is highly suitable for repair and remodeling projects, where its ease of use and non-reactive nature can simplify application processes without sacrificing reinforcement quality.
Understanding these types and their applications can significantly enhance project outcomes. Practical experience shows that selecting the right wire mesh takes into account the environmental conditions, specific concrete structure requirements, and future durability expectations. As professionals with extensive experience in construction material optimization can attest, making an informed selection of wire mesh involves balancing initial costs with long-term benefits, ensuring the sustainability and success of your concrete projects.