Steel grating plates, often overlooked in the broader construction and industrial landscape, represent a backbone of robust infrastructure. From factories to pedestrian walkways, these unsung heroes provide safety, durability, and versatility. My journey through the multifaceted world of steel grating plates revealed insights rooted in experience and guided by a fervent commitment to marrying functionality with quality.
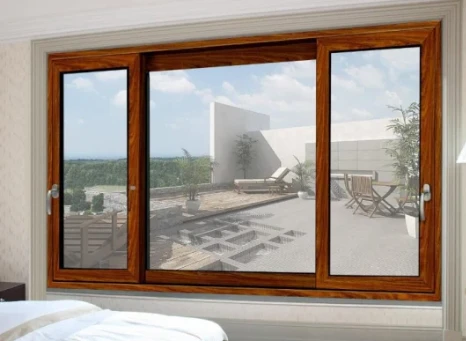
Years ago, when I first delved into the intricacies of construction materials, the sheer strength and adaptability of steel grating plates were compelling. What distinguishes these plates is their adeptness at providing sturdy flooring solutions that withstand immense weight and prolonged usage. My expertise in structural engineering armed me with an analytical lens through which I assessed their patterns, materials, and load-bearing capacities.
Steel grating plates come primarily in two forms welded and press-locked, each offering distinct advantages. The welded variant is revered for its strength due to intersecting bars fused by high-pressure resistance welding. On the other hand, the press-locked grating combines aesthetic appeal with functional integrity, achieved by pressing the load-bearing bars and cross bars together under immense power. Understanding the nuanced differences between these types informed my guidance to clients and partners on optimal selections based on specific project requirements.
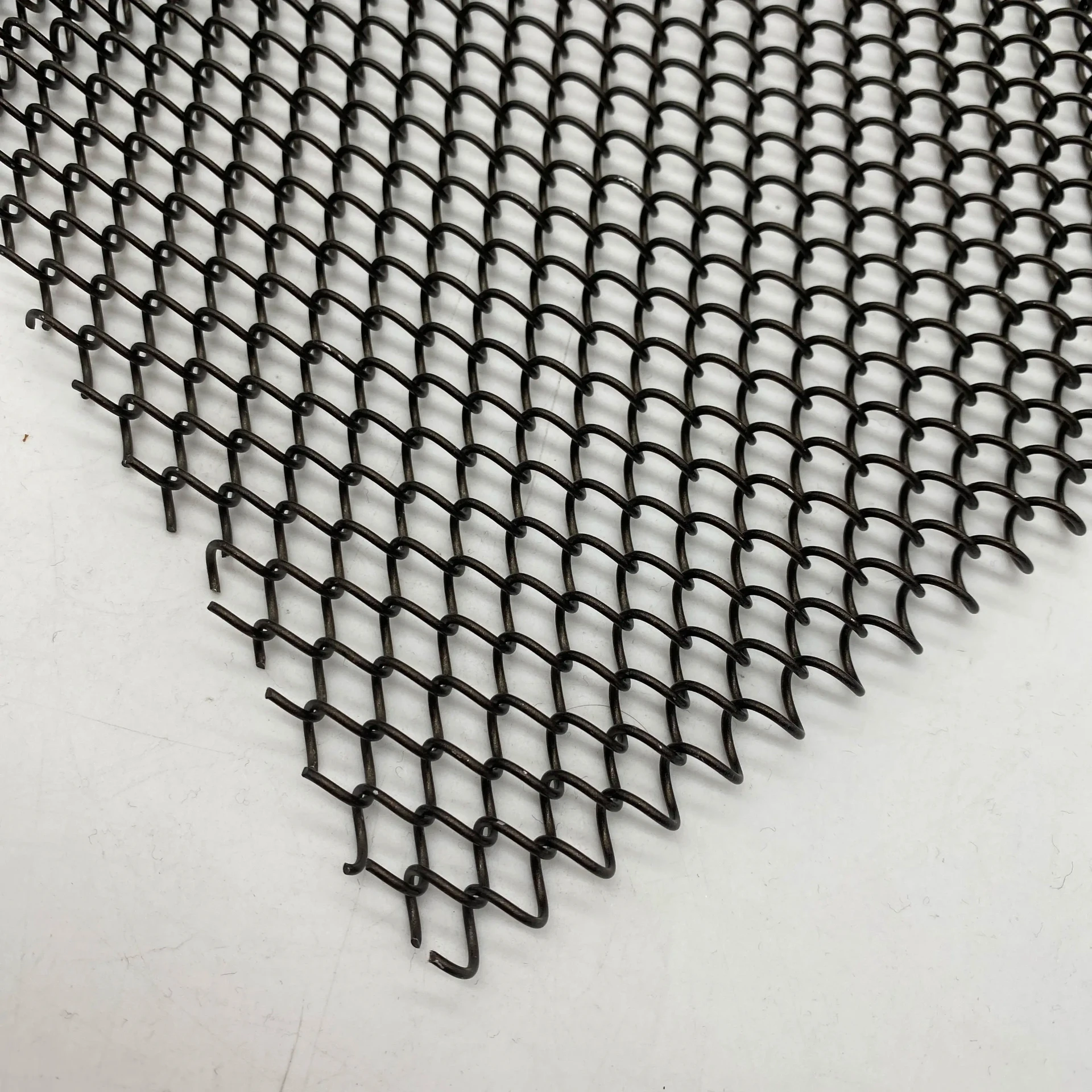
Expertise in this domain demands attention not just to structural properties but also to environmental adaptability. Galvanization of steel grating plates significantly enhances resistance to rust and corrosion - a crucial component when considering longevity, particularly in outdoor or moisture-laden settings. I recall working on a seaside industrial complex where the corrosive salinity of the environment posed a significant threat. Employing hot-dip galvanized steel grating eliminated potential degradation, ensuring both longevity and reduced maintenance costs.
steel grating plate
Authoritativeness in the field is not solely about understanding product specifications but also about comprehending their applications across diverse settings. Steel grating plates offer remarkable versatility, from walkways and mezzanines in factories to ventilation grates in urban landscapes. A noteworthy implementation involved a bustling metropolitan train station where we utilized lightweight, yet immensely strong, aluminum steel grating plates to revitalize aging pedestrian bridges. The result was enhanced safety for thousands of commuters and a leap in aesthetic appeal without sacrificing functionality.
Trustworthiness, however, is the bedrock on which all constructive endeavors rest.
Suppliers and manufacturers play a pivotal role in maintaining product integrity. My collaborations have always stressed the importance of sourcing from reputable vendors committed to rigorous quality standards. Certifications, including those complying with ISO and ASTM standards, serve as indispensable markers of trust that inform decision-making processes.
In practice, choosing the right steel grating plates transcends mere technical specifications. Real-world testing alongside rigorous quality assurance processes fortifies the decision-making pipeline. Having witnessed failures and triumphs, my conviction lies in urging decision-makers to prioritize accredited quality checks and real-world simulations in their procurement strategies.
On a closing note, steel grating plates are not just components in the architecture of infrastructure—they are pivotal players ensuring safety, stability, and efficiency. My hands-on experiences and dedicated study of material sciences stand testament to the transformative role they play. As we continue to innovate and adapt to evolving architectural demands, the humble steel grating plate will persist as a cornerstone of modern engineering solutions.