Exploring the intricate world of steel grating details unveils an array of fascinating insights that marry functionality with architectural aesthetics. Steel grating is an essential component in numerous applications, from industrial flooring to walkway panels, demanding a close examination by professionals well-versed in materials science and structural engineering.
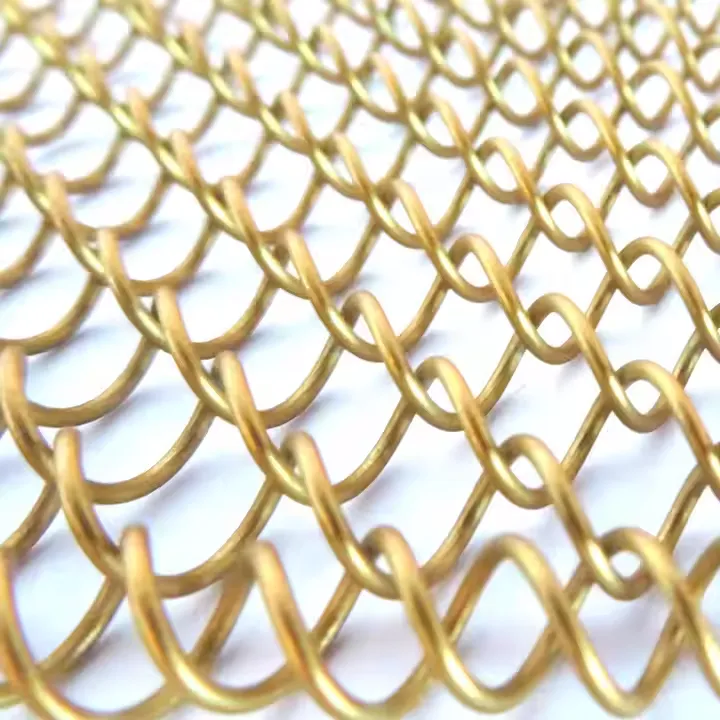
Steel grating, known for its robust characteristics, is categorized mainly into two types welded and press-locked. Welded steel grating is constructed using automated forge-welding that joins the cross bars and bearing bars, achieving a fusion of immense strength. Traditionally, this type of grating is favored in environments that require exceptional load-bearing capabilities, such as factory floors and bridges. On the other hand, press-locked grating is engineered through precise mechanical pressure, interlocking the bars to create a cleaner look often sought in architectural designs.
The essence of understanding steel grating details lies not only in its manufacturing process but also in the selection of the appropriate material. Commonly, steel grates are made from carbon steel, stainless steel, or aluminum, each bearing unique properties that cater to specific conditions. Carbon steel offers affordability and versatility,
making it a staple in heavy-duty applications. Meanwhile, stainless steel grating is celebrated for its resistance to corrosion and ability to maintain structural integrity in adverse weather conditions, making it suitable for marine environments. Aluminum, known for its lightweight characteristic and corrosion resistance, often finds favor in applications where weight is a consideration, such as in the transportation industry.
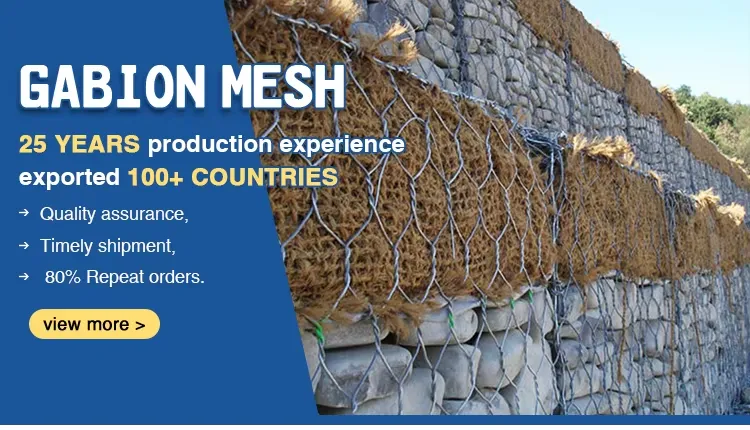
Detailing the considerations for selecting the correct steel grating specifications further reveals an industry steeped in precision and expertise. Load-bearing capacity, span, bar size, and grating height are critical factors that impact performance. For instance, selecting a lower gauge steel for applications with excessive loads can result in compromise of safety and efficacy, making it imperative for engineers to meticulously calculate these variables.
steel grating details
Moreover, professionals must pay heed to the finish of steel grating, which adds a layer of defense against wear and exposure. Galvanized finishes, achieved by submerging the steel in molten zinc, offer a formidable barrier against rust and enhance longevity, especially in outdoor placements. For environments that demand enhanced aesthetics alongside functionality, painted or powder-coated finishes allow customization that complements the surrounding architecture while providing additional protection.
Practical experience in the field underscores the necessity for compliance with industry standards and regulations. Understanding and adhering to guidelines such as those provided by the American National Standards Institute (ANSI) or the Occupational Safety and Health Administration (OSHA) ensures that installations not only meet safety standards but also uphold quality benchmarks recognized globally.
The emergence of advanced manufacturing techniques has further propelled the steel grating industry forward, spurring innovations such as serrated grating, which enhances slip resistance—a critical feature for safety-conscious industries. Serrated grating sees frequent use in oil rigs, chemical plants, and other industrial settings where worker safety is paramount. The advent of software-assisted design tools has equally empowered engineers to simulate grating performance under various stresses, leading to more informed decision-making processes in projects of all scales.
In conclusion, the depth of expertise required to navigate steel grating details elevates the discipline to both an art and a science, demanding a comprehensive understanding of materials, engineering principles, and safety standards. Those in the industry, equipped with extensive knowledge and experience, play a crucial role in ensuring that steel grating not only fulfills its utilitarian purpose but also contributes aesthetically and safely to the infrastructure that supports our modern world. This confluence of expertise underscores the continued relevance and authority of steel grating in diverse applications across the globe.