Serrated gratings often conjure images of robust architectural spaces and industrial applications, where their quintessential role cannot be overstated. The variety in serrated grating sizes directly impacts their applicability, effectiveness, and efficiency across different sectors. To truly grasp the significance of choosing the correct serrated grating size, it's essential to explore detailed insights from industry experience and expertise.
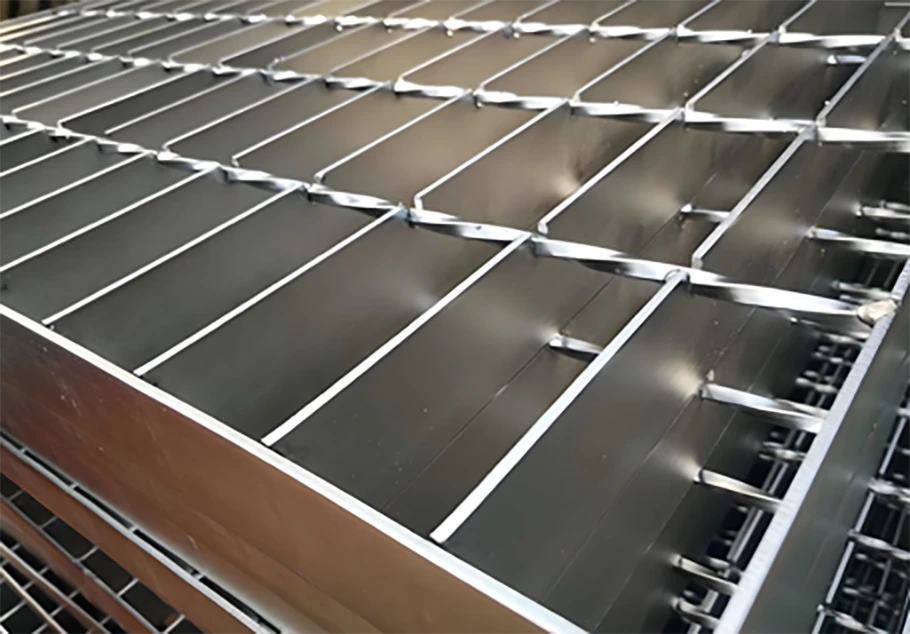
The essence of serrated gratings lies in their ability to offer superior slip resistance, a feature critical in environments where safety is paramount. Industries with rigorous safety standards, such as oil and gas, shipping, and manufacturing, often rely on these gratings to ensure workplace safety. The choice of grating size is crucial here, as it influences the load-bearing capacity and the level of grip or anti-slip functionality required for specific tasks. Smaller serrations typically provide increased grip, beneficial in environments exposed to oil, chemicals, or wet conditions. Larger serrations, meanwhile, can offer robust support for equipment and hefty foot traffic.
From an engineering perspective, the variable sizes of serrated gratings allow for customization to meet precise industrial requirements. For instance, in petrochemical plants, gratings with larger serrations might be used in areas requiring easy drainage of liquids, while smaller serrations could be suited for pathways and walkways where pedestrian safety is a priority. A professional consultation with structural engineers can provide tailored solutions that consider the load expectations and environmental factors unique to each project.
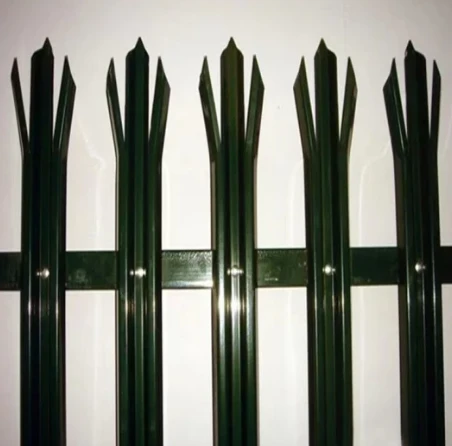
Authoritatively addressing the selection process involves understanding the materials used alongside grating size. Common materials include steel, stainless steel, and aluminum, each affecting the overall weight and durability of the grating. In environments prone to corrosion, stainless steel serrated gratings are often preferred for their longevity and resistance to rust. However, for less severe environments, carefully calibrated steel or aluminum gratings offer cost-effective alternatives without compromising on quality and performance.
serrated grating sizes
Experience has shown that incorrect grating size can lead to either under-utilized or overburdened surfaces, raising maintenance costs and presenting potential safety hazards. Hence, it's vital to engage with suppliers who not only possess a comprehensive catalog of grating sizes but also the expertise to guide decision-making processes. Top suppliers in this field maintain a variety of grating sizes and provide customization options to fit specific requirements, ensuring that all safety, structural, and economical aspects are considered.
Trustworthiness in this industry is anchored by quality certifications and adherence to international safety standards such as ISO 9001. Selecting gratings from certified manufacturers guarantees a baseline of manufacturing quality and product reliability. It's these trusted manufacturers who frequently participate in trade shows, share white papers, and are involved in industry discussions, solidifying their authority and commitment to delivering top-tier products.
For those embarking on projects requiring serrated grating, understanding these elements—from serration size and material choice to supplier credibility—is paramount. By leveraging expert consultations and industry resources, businesses can enhance their infrastructures safely and efficiently with the right serrated grating solutions.