Hot dip galvanized grating stands out as an indispensable component in the construction and industrial landscape, renowned for its durability, corrosion resistance, and multifaceted applications. As the demand for robust and long-lasting materials continues to surge, understanding the factors that make hot dip galvanized grating an optimal choice becomes imperative for industry professionals seeking to maximize their return on investment.
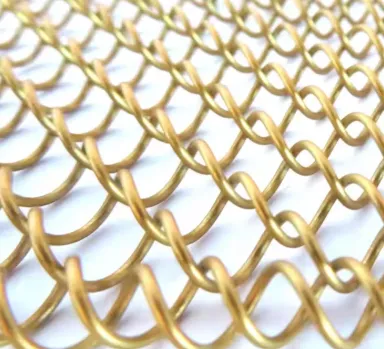
The process of hot dip galvanization involves immersing the steel grating into a bath of molten zinc, ensuring comprehensive coating and enhanced protection against corrosion. This process is fundamentally superior to other galvanization methods because it provides a thick, uniform coating that wards off rust and corrosion for extended periods. This longevity is particularly vital in environments exposed to harsh elements, such as marine settings or industrial sites where chemical exposure is common.
A key advantage of hot dip galvanized grating is its exceptional durability. The zinc coating offers a protective barrier that not only resists corrosion but also increases the grating's overall lifespan, translating into significant cost savings over time. This makes it an ideal material for infrastructure projects that demand both initial performance and long-term sustainability, such as bridges, platforms, and walkways.
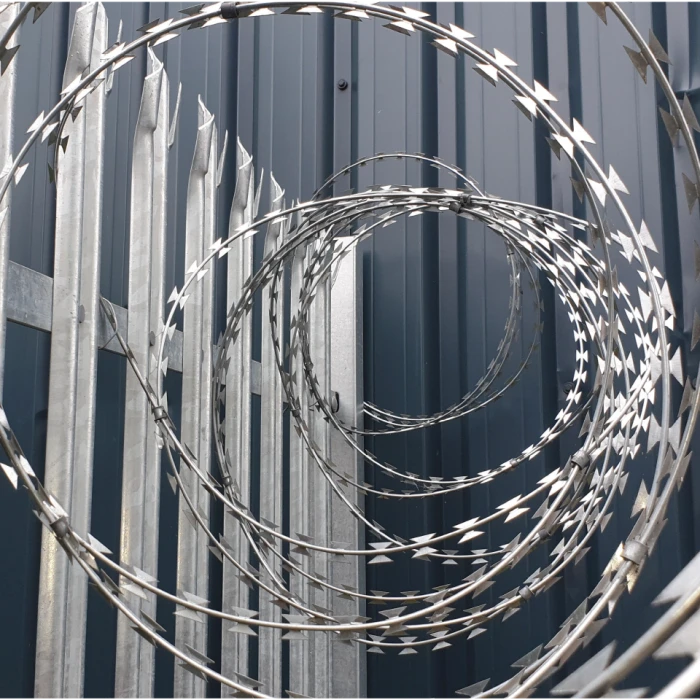
The expertise embedded in producing hot dip galvanized grating cannot be understated. Manufacturers prioritize quality control throughout the galvanization process, adhering to stringent industrial standards to ensure each piece meets the desired performance criteria. This level of expertise extends to the technical design of the grating itself, where understanding load-bearing capacities and structural integrity are crucial. This is particularly important in applications where safety and reliability are paramount, underscoring the grating’s relevance in both public and private sector projects.
hot dip galvanized grating
Furthermore, the versatility of hot dip galvanized grating aligns well with its extensive array of applications. From being used in ceiling grids and flooring solutions to supporting heavy machinery on industrial sites, the adaptability of this material is a testament to its engineering excellence. The customizable nature of the grating allows for adjustments in terms of size, thickness, and pattern, catering to specific project requirements and contributing to its widespread use across different industries.
Authoritativeness comes into play through the grating’s compliance with international standards. Products that carry certifications and meet established benchmarks foster confidence among consumers and industry professionals, reinforcing their status as reliable and high-quality solutions. Companies specializing in hot dip galvanized grating often boast a track record of successful projects and satisfied clients, further cementing their authority in the field.
The trustworthiness of hot dip galvanized grating is bolstered by its predictability and consistency in performance. Choosing a grating solution that has been tried and tested in various conditions assures project managers and engineers that they are investing in a product with proven resilience. This trust is not just rooted in the product’s physical characteristics, but also in the technical support and warranties often provided by reputable manufacturers, ensuring ongoing support and commitment to quality.
In conclusion, hot dip galvanized grating emerges as a paragon of innovation and practicality in material science. Its synthesis of durability, expertise-driven design, compliance with standards, and flexible functionality renders it invaluable in an ever-evolving industrial landscape. As more entities seek materials that withstand the test of time and elements, hot dip galvanized grating continues to be a prudent choice that upholds the principles of sustainability and efficiency.