Galvanized serrated bar grating has become an essential component in various industrial and architectural applications, known for its strength, durability, and slip-resistant properties. These gratings, often fabricated from steel or aluminum, undergo a galvanization process that enhances their lifespan and corrosion resistance. The serrated surface provides an extra layer of safety, making it ideal for environments where traction is paramount, such as walkways and platforms in factories, refineries, and plants.
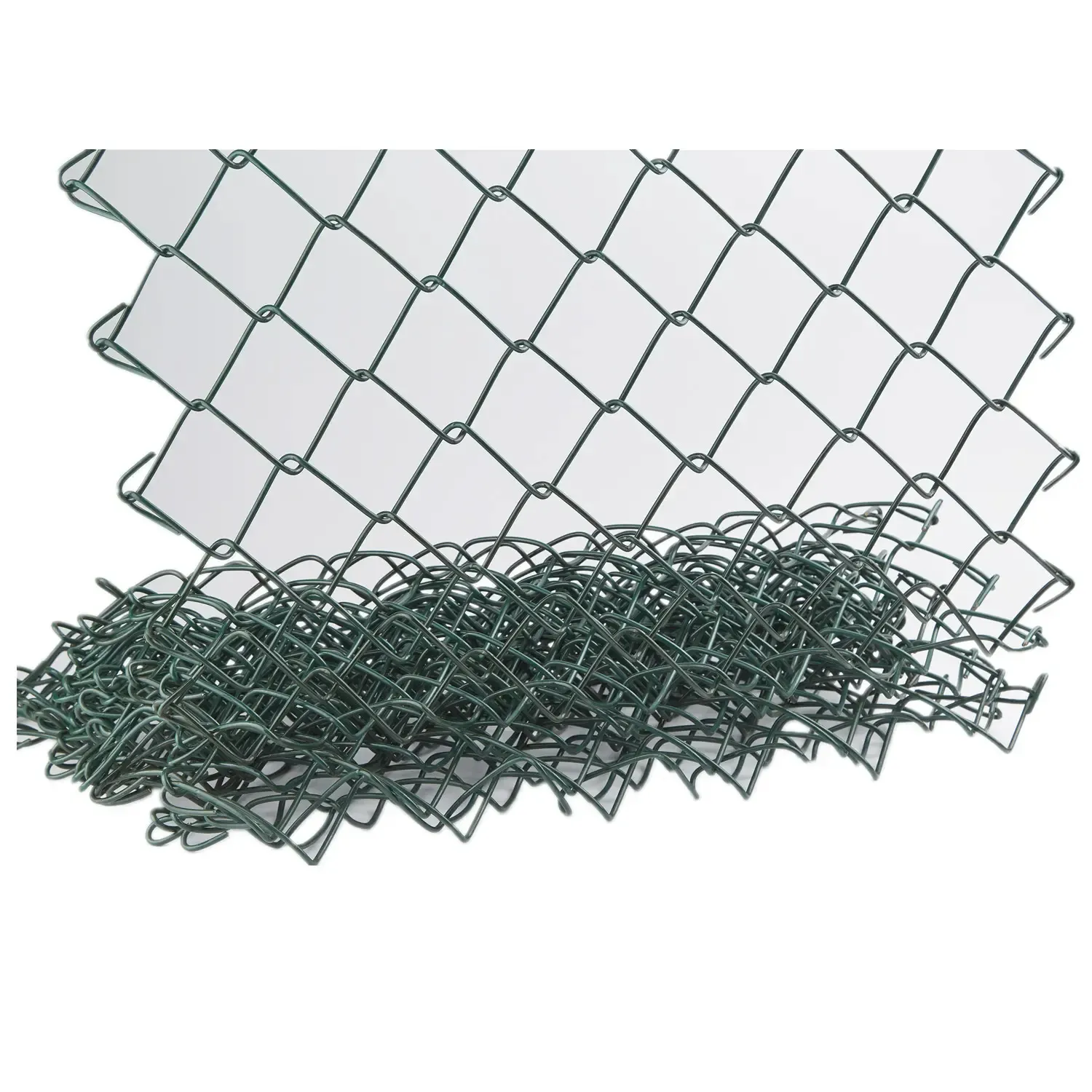
When choosing galvanized serrated bar grating, it is crucial to consider the load requirements and the environmental conditions in which the grating will be used. For industrial settings that experience heavy foot traffic or machinery movement, selecting a grating with the appropriate thickness and spacing is essential. Moreover, in corrosive environments, such as those exposed to saltwater or chemicals, galvanized options outperform other materials due to their protective zinc coating that prevents rust and deterioration.
The expertise involved in manufacturing these gratings cannot be overstated. The process begins by welding or pressure-locking steel or aluminum bars to form a grid structure with serrated edges. The welds ensure strength and integrity,
while the serrated surface enhances grip. Following fabrication, the grating is dipped in molten zinc, creating a metallurgical bond that coats the bars thoroughly. This galvanization process not only protects against rust but also adds to the overall robustness of the product, making it suitable for harsh outdoor conditions.
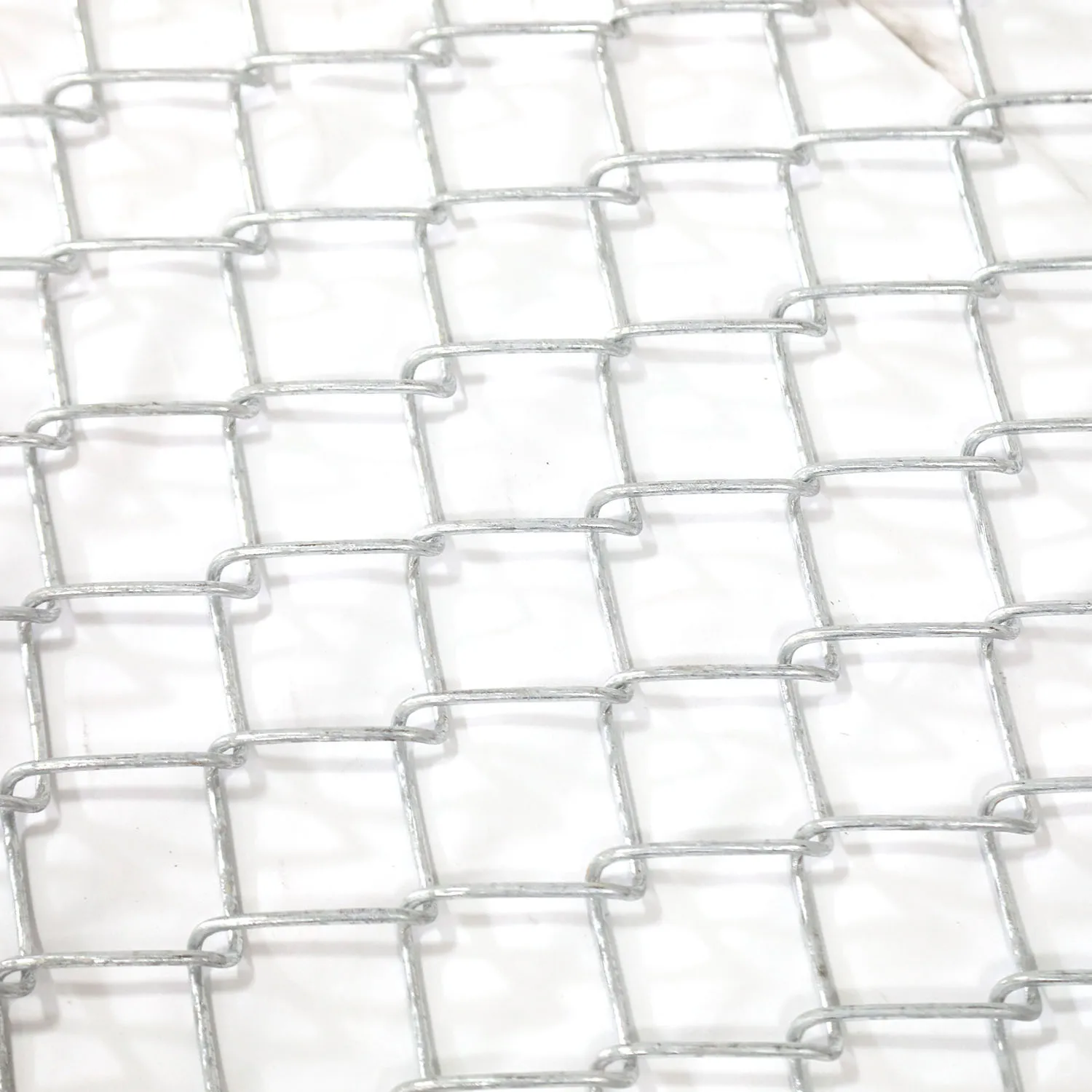
From an authoritative perspective, galvanization standards, such as those outlined by the American Society for Testing and Materials (ASTM), ensure that the gratings meet specific quality and safety benchmarks. Products that comply with these standards provide users with the confidence that the gratings will perform as expected in demanding applications. These standards cover aspects such as the thickness of the zinc coating, the method of application, and the quality of the steel or aluminum used, reinforcing the credibility of the grating's durability and longevity.
galvanized serrated bar grating
A true testament to the trustworthiness of galvanized serrated bar grating is their widespread use across various sectors—ranging from industrial facilities to architectural highlights. One notable example includes their installation in urban infrastructure projects, where pedestrian safety is paramount. Here, the gratings not only function as a security measure but also enhance the aesthetic appeal of public spaces, demonstrating a balance between functionality and design.
To maximize the performance and lifespan of galvanized serrated bar grating, maintenance practices should be implemented consistently. Regular inspections for surface buildup of debris or dirt can prevent blockages that may affect drainage or corrosion resistance. With proper care, the lifecycle of these gratings can be extended, ensuring continued effectiveness and safety for years.
Overall, galvanized serrated bar grating offers a reliable solution for many industries, combining the critical factors of safety, durability, and resilience. As more sectors recognize the value of integrating such robust materials, the demand for high-quality, expertly crafted grating continues to grow. Experts in the field consistently emphasize the importance of understanding both the material properties and the specific environmental conditions to make informed decisions regarding grating selection and application.