Understanding the factors that affect the price of galvanized grating is crucial for construction managers, engineers, and procurement specialists. Galvanized grating, known for its durability and corrosion resistance, is widely used in industrial floors, stair treads, platforms, and drainage covers. However, the cost of this indispensable material can vary significantly. Below, we dissect the unique features of galvanized grating prices, providing valuable insights from an experienced perspective.
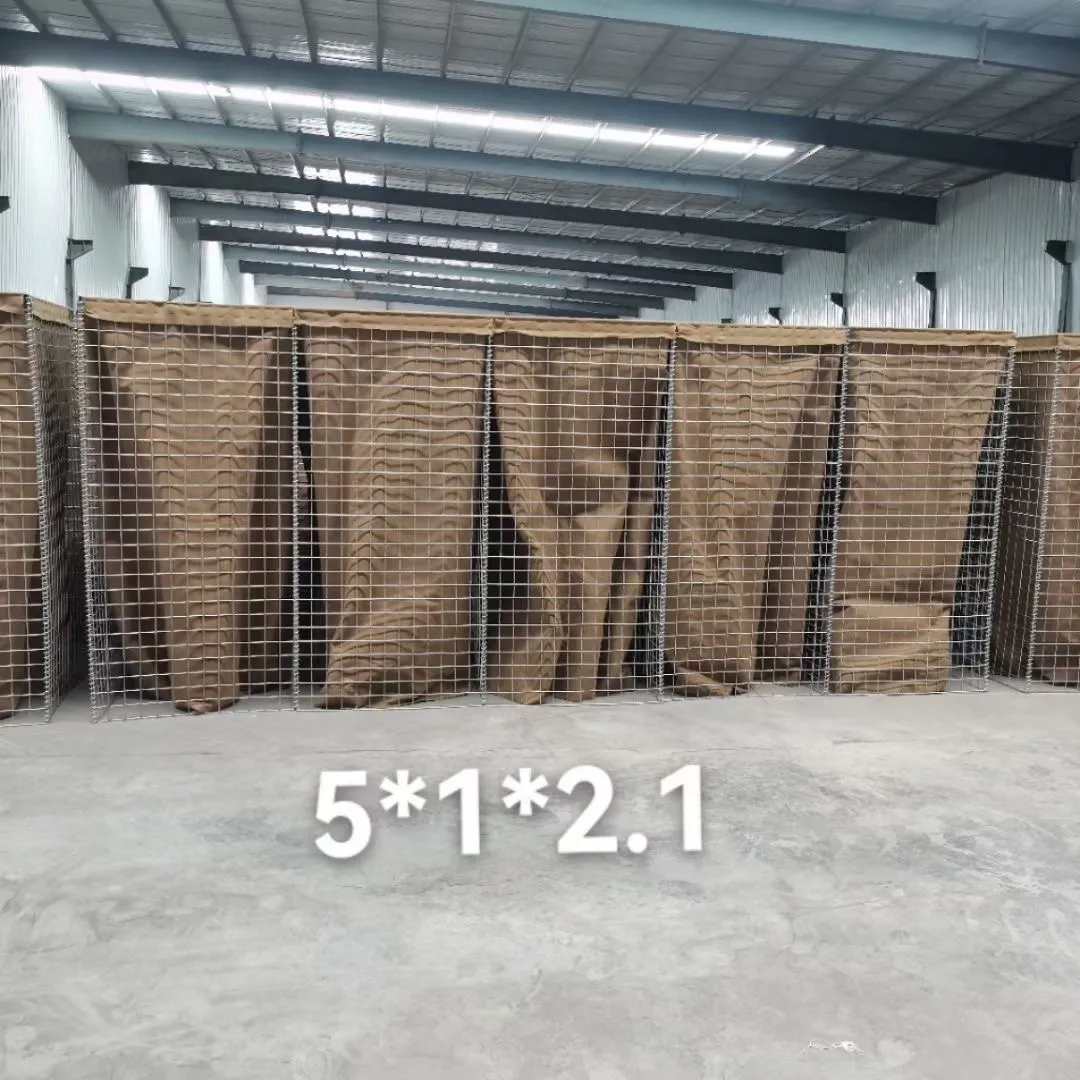
The price of galvanized grating is influenced primarily by the material costs. Steel is the fundamental component in grating, and its market price is subject to fluctuations based on global supply and demand. Factors such as geopolitical tensions, trade tariffs, and natural disasters can affect steel prices, subsequently impacting grating costs. Monitoring steel markets regularly provides the foresight necessary to anticipate these fluctuations and make informed purchasing decisions.
Moreover, the process of galvanization—applying a protective zinc coating to prevent corrosion—adds additional cost. The price of zinc is also variable, dependent on mining outputs, export regulations, and technological advances in mining and processing. Understanding the synchronization between steel and zinc market trends is essential for stakeholders looking to optimize their expenditure on galvanized grating.
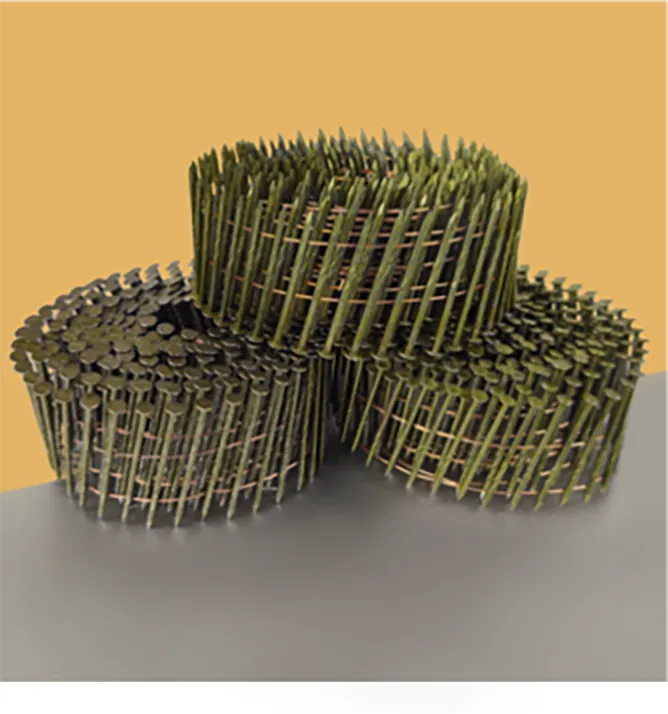
Product specifications play another critical role in determining price. This grating comes in a variety of sizes, thicknesses, and spacing patterns, each suited for different applications and load-bearing requirements. Larger or custom-sized gratings typically incur higher costs due to increased material usage and customized manufacturing processes. For instance, heavy-duty gratings designed to bear substantial weight require more robust materials and thicker coatings, thus commanding a higher price point.
galvanized grating price
It's also worthwhile considering the production method used to create the grating. Welded grating, press-locked grating, and swaged grating each have distinct manufacturing processes that influence cost. Welded grating, often less expensive, offers high strength and stability, ideal for most industrial applications. In contrast, press-locked grating, known for its precision and adaptability, and swaged grating, noted for its lightweight yet steady nature, might be more costly due to the additional labor and expertise involved in their production.
Transportation and logistics further impact the final price of galvanized grating. As a heavy and bulky material, shipping costs can be substantial, particularly for remote project sites. Selecting local suppliers or leveraging logistical partnerships can help mitigate these costs. Additionally, bulk purchasing often results in discounts, providing opportunities for cost savings if aligned with project timelines.
Experience from industry veterans highlights that market timing is another decisive factor. Engaging with suppliers during low-demand periods can lead to advantageous pricing due to excess inventory or reduced competition. Similarly, cultivating long-term relationships with suppliers can offer benefits such as priority access to stock and pre-negotiated discounts, fostering a mutually beneficial partnership.
In conclusion, understanding the price dynamics of galvanized grating requires a multi-faceted approach, integrating market analysis, technical specifications, and strategic supply chain management. Experience and expertise in these areas not only ensure cost-effective procurement but also contribute to project success by securing high-quality materials. By prioritizing authoritativeness and trustworthiness in supplier relationships and staying informed about market trends, decision-makers can confidently navigate the complexities of galvanized grating pricing.