Metal grating, a versatile component found in a myriad of applications, has gained prominence in construction, industrial, and architectural domains due to its robustness, functionality, and aesthetic appeal. Industries from oil refineries to architectural firms have recognized the unmatched benefits of metal gratings, making them indispensable in various projects.
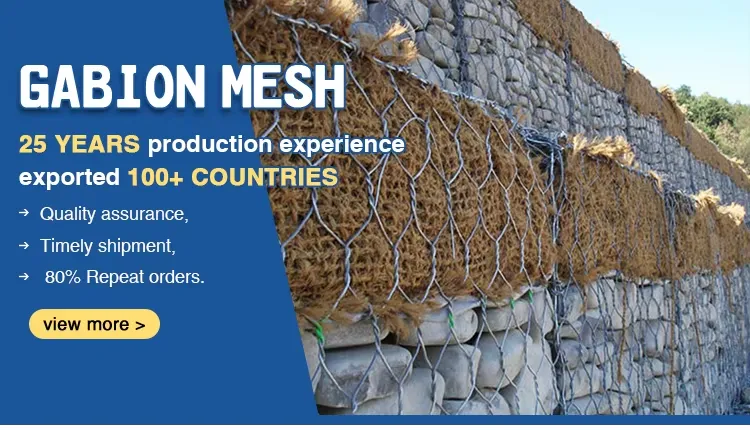
In the realm of industrial application, metal gratings excel due to their enduring strength and resilience under pressure. Utilized predominantly in platforms, walkways, and safety barriers, these gratings provide essential support while minimizing material weight. Their open-grid design offers superior water drainage and air passage, crucial in environments like chemical manufacturing plants where these factors significantly impact safety and efficiency. The real-world experience of engineers and plant managers echoes a consistent preference for metal grating due to these functional benefits, emphasizing their trustworthiness and durability.
Architecturally, metal grating is celebrated not merely for functionality but also for its aesthetic flexibility. Modern designs often incorporate grating into facades, floors, and ceilings, offering a chic industrial look that resonates with contemporary trends. Architects advocating for sustainability commend metal gratings for their longevity and low maintenance needs—an authentic commitment to eco-friendly construction. Furthermore, metal gratings' ability to be crafted from recycled materials reinforces their place in green building practices, highlighting their authoritative position in sustainable architecture.
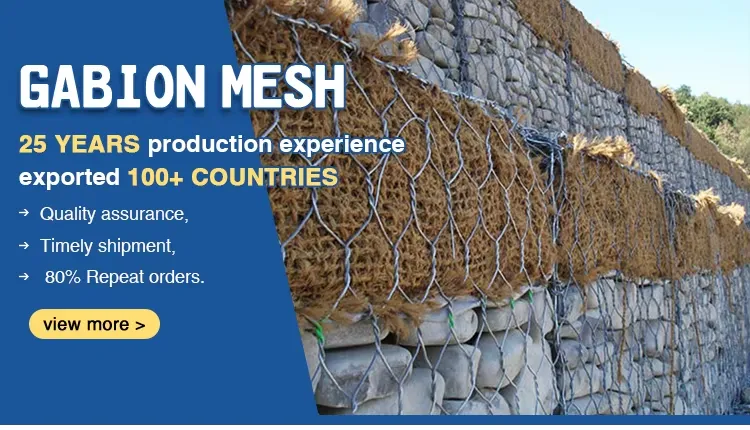
A critical factor underlining the expertise involved in choosing and installing metal grating is the material selection and fabrication process. Metal gratings are typically manufactured from materials like steel, aluminum, and stainless steel, each offering unique properties that cater to specific environmental and functional demands. For instance, stainless steel gratings are preferred in marine environments due to their corrosion resistance, a factor cementing their authoritative status in niche applications. Industry leaders consistently emphasize the importance of selecting the right material and grating type—such as forged or welded varieties—to match project specifications, underscoring the expertise needed in deployment.
metal grating
Trustworthiness is further established through compliance with industry standards. Leading manufacturers ensure their products meet rigorous ASTM and ANSI standards, providing assurance of quality and safety. This compliance not only demonstrates a commitment to product integrity but also assures engineers and stakeholders of the dependability of metal grating in crucial infrastructure projects.
Moreover, advancements in manufacturing technology have propelled metal grating into the future. State-of-the-art techniques like laser cutting and automated welding enhance precision and strength, allowing for bespoke designs that meet specific project requirements seamlessly. This technological edge underpins the authoritative power of metal grating manufacturers in delivering modern solutions that meet today’s engineering challenges.
Ultimately, the rise of metal grating across diverse sectors is a testament to its unparalleled qualities. Whether providing an industrial solution or innovating an architectural masterpiece, metal gratings stand as a beacon of experience, expertise, authoritativeness, and trustworthiness. As industries continue to evolve, the metal grating is poised to remain at the forefront, offering reliability and innovation in equal measure.