Floor grating has emerged as a fundamental component in various industrial and commercial applications, offering versatility and durability. Identifying the right floor grating solution is pivotal to ensure operational efficiency and safety. With firsthand experience and extensive knowledge in the field, it is essential to delve deep into its practical applications and benefits.
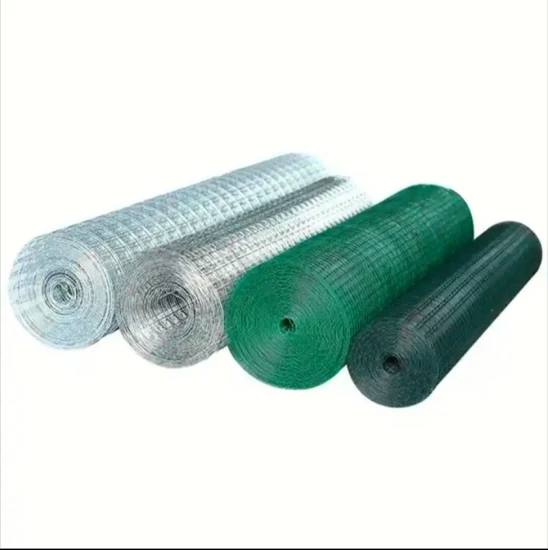
Floor grating often finds its use in manufacturing plants, walkways, platforms, and drainage covers due to its robust construction. Made from materials like steel, aluminum,
or fiberglass, each type offers distinct advantages. Steel grating, for instance, is celebrated for its strength and load-bearing capacity, making it ideal for heavy-duty environments. Aluminum, on the other hand, brings in the benefits of being lightweight and corrosion-resistant, which is perfect for areas where ease of handling and long-term resistance are crucial. Fiberglass, with its non-conductive and non-corrosive nature, offers a perfect alternative in chemically aggressive or wet environments, ensuring safety without compromising on longevity.
An in-depth understanding of floor grating design and how it caters to particular needs reinforces expert knowledge in this domain. The design of the grating impacts not only its functionality but also its safety features. Opting for serrated surfaces can significantly reduce slip risks, while mesh sizes determine the load distribution capabilities and debris clearance. Industries that deal with oil, chemicals, or food processing particularly benefit from custom designs that prevent workplace hazards and maintain hygiene standards.
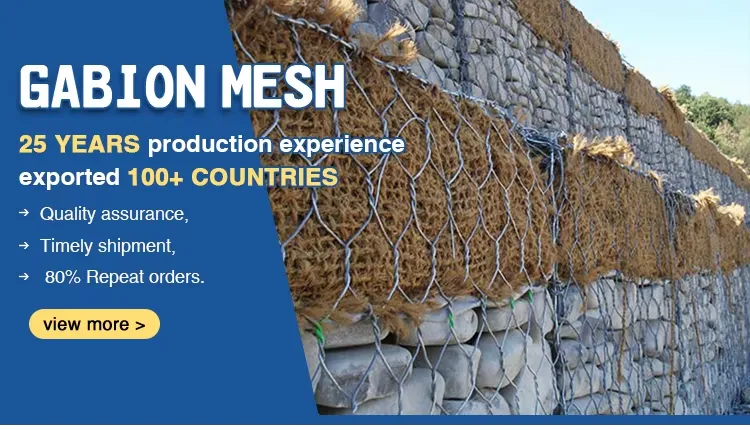
Trustworthiness in selecting and installing floor grating systems comes from relying on reputable manufacturers who adhere to industry standards and regulations. A detailed scrutiny of product certifications, load testing results, and compliance with OSHA guidelines is imperative. This not only ensures the product's credibility but also its long-term performance in demanding environments.
floor grating
The authoritativeness of any recommendation regarding floor grating is reinforced by real-world performances and case studies. Numerous sectors have reported substantial improvements in operational safety and maintenance costs after switching to customized floor grating solutions. For example, a large-scale beverage manufacturer successfully minimized slip accidents and improved maintenance downtime by incorporating fiberglass grating on their production floors, highlighting the direct impact of choosing the right material and design.
Finally, fostering trust between providers and clients involves transparent dialogue about specific needs and challenges, offering tailored solutions rather than one-size-fits-all products. By employing a consultative approach in floor grating selection, businesses can achieve optimal results, ensuring both employee safety and operational efficiency remain uncompromised.
Continual advancements in material science and engineering pave the way for innovative developments in floor grating solutions, promising to meet the evolving demands of various industries while upholding the highest standards of safety and efficacy.