When considering the purchase of galvanised grating, understanding the factors influencing its pricing can significantly benefit both seasoned buyers and newcomers. For those unfamiliar, galvanised grating offers unmatched strength and durability, thanks in part to the galvanisation process which involves coating the steel with zinc. This process not only enhances its resistance to rust and corrosion but also extends its longevity, making it an ideal choice for various industrial and commercial applications.
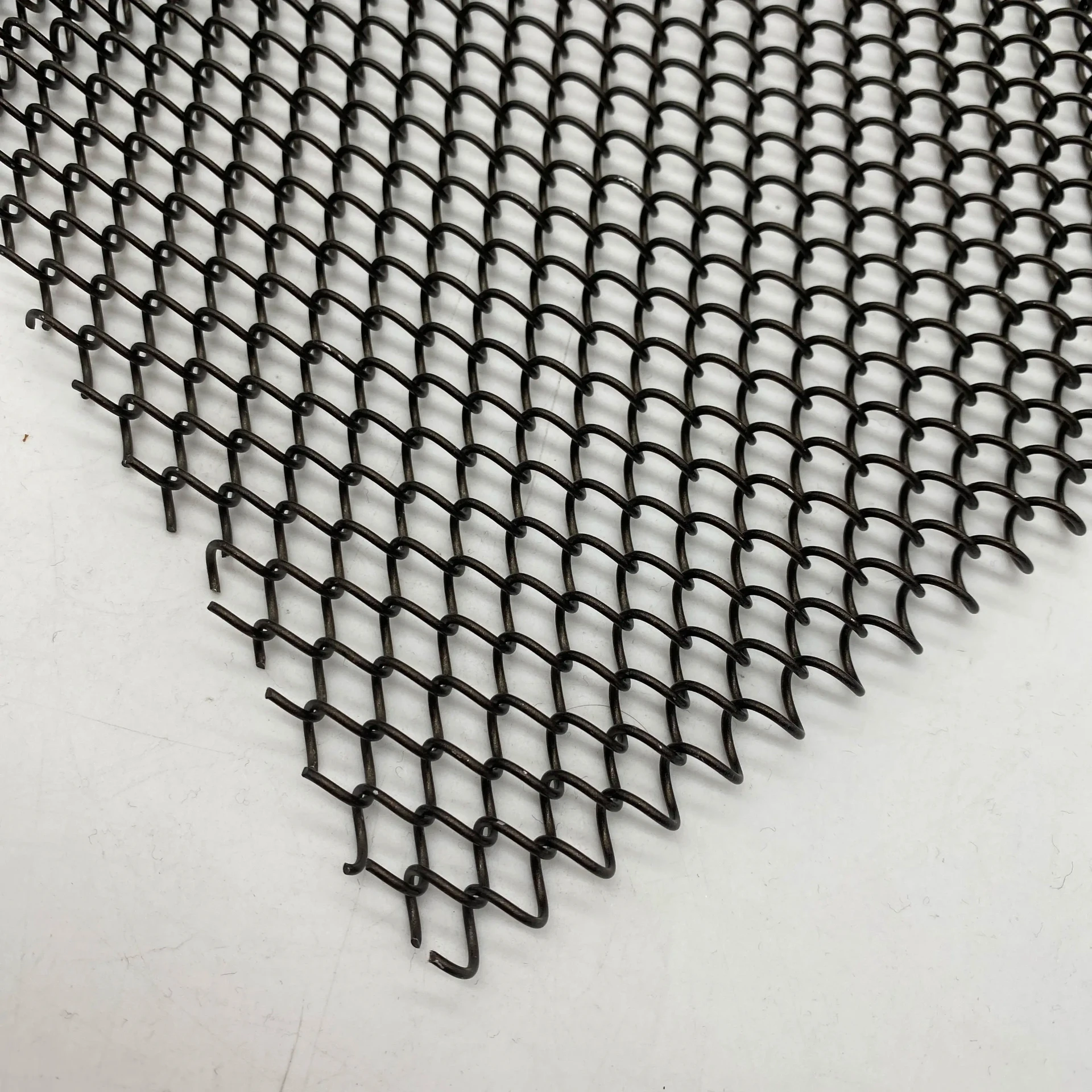
Pricing for galvanised grating can vary widely based on multiple variables, each playing a critical role in the final cost. First and foremost is the type of material used. Galvanised grating primarily comes in two types—carbon steel and stainless steel. While carbon steel is cost-effective and provides ample strength, stainless steel offers superior corrosion resistance and aesthetic appeal, albeit at a higher price.
Another crucial factor is the size and shape of the grating. Standard size panels are generally more affordable due to mass production, while custom sizes or intricate shapes might incur additional costs due to custom fabrication requirements. Thickness and load-bearing capacity also add to the price. Thicker gratings capable of supporting heavier loads consume more raw material and require more robust galvanisation, thereby increasing costs.
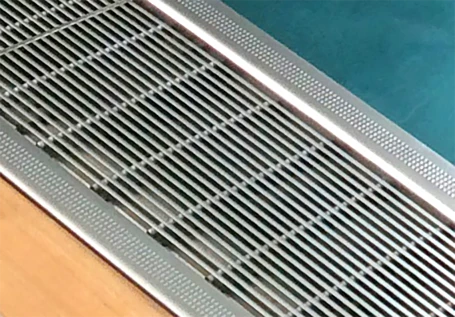
The method of galvanisation significantly affects price. Hot-dip galvanisation, the most common method, provides a thick, durable coating and is generally more cost-effective for large gratings. Electro-galvanisation, on the other hand, offers a thinner coat suitable for lighter applications but may be preferred in specific industrial contexts due to its smoother finish.
Market conditions can also impact the price. The cost of zinc, a key component in the galvanisation process, can fluctuate based on market demand and supply dynamics. Similarly, local economic conditions, including tariffs and trade policies, can influence both global and regional pricing structures.
galvanised grating price
A practical tip when purchasing galvanised grating is to consider the supplier's reputation and service offerings. Established suppliers often provide assurances of quality and consistency, backed by certifications and standards compliance, such as ISO certifications. Additionally, factors such as delivery time, availability of stock, and after-sales support should be assessed. Suppliers with a track record of reliability can sometimes justify a premium price, reflecting the added value of peace of mind and guaranteed product performance.
Incorporating personal experience or testimonials into the purchasing process can also be invaluable. Engaging with community forums or industry networks can yield insights into not only pricing but also product performance in real-world applications. Reviews and case studies often reveal nuanced experiences that a price tag alone cannot convey, emphasizing aspects like ease of installation, wear over time, and customer service interactions.
Finally, it's vital to align the product choice with the specific requirements of the installation environment. For instance, environments with high exposure to saltwater or chemical spills might necessitate higher-grade stainless steel or additional coatings, therefore influencing the cost. A precise understanding of the environmental demands will ensure optimal performance of the grating and justify the investment.
In conclusion, purchasing galvanised grating involves a delicate balance between cost and functional requirements. By considering material type, size, galvanisation method, market conditions, and supplier credentials, buyers can secure a product that offers both economic and functional advantages. Thorough market research combined with expert advice and real-world testimonials can lead to a more informed purchase, ensuring the best value for money and long-term satisfaction with the product.