Bar grating dimensions are a crucial consideration for any project involving industrial flooring, walkways, and platforms. This article delves deep into the nuances of selecting the perfect bar grating, focusing on experience, expertise, authoritativeness, and trustworthiness in this specialized field.
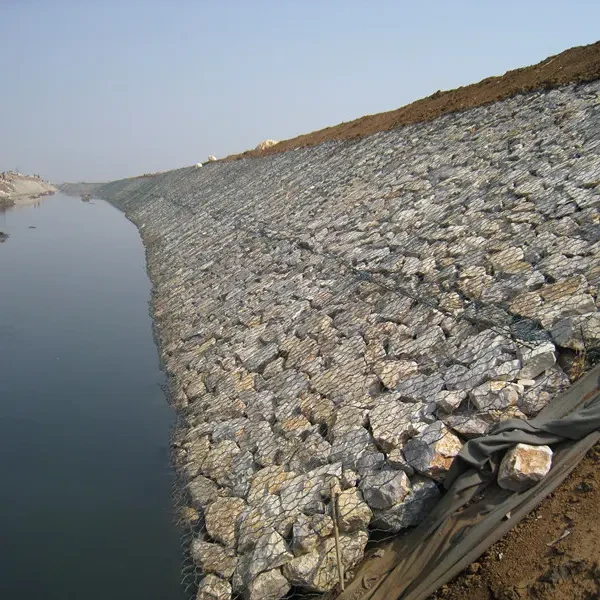
Bar gratings come in a myriad of dimensions, each tailored to specific applications. The common variants include flat bar gratings, serrated, and I-bar types, which are selected based on load requirements, safety standards, and project-specific needs. When choosing bar grating dimensions, one must consider the span conditions and load-bearing capabilities. Typically, these gratings are measured by bearing bar size, that is, the height and thickness of the bearing bars – crucial components providing structural strength.
From a professional standpoint, understanding the intricacies of bearing bar spacing is critical. The standard spacing options, such as 19-w-4, 15-w-4, and 11-w-4, specify the center-to-center distance between bars. These dimensions directly influence the strength and aesthetic of the grating. Experience in the field shows that the 19-w-4 spacing is highly popular due to its balance between economy and load capacity, effectively serving areas with moderate load requirements such as pedestrian walkways.
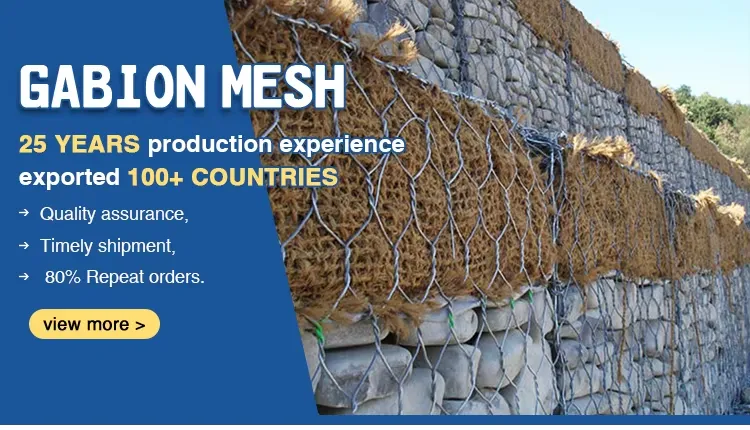
A key aspect of ensuring the effectiveness and safety of bar gratings involves comprehension of load tables provided by manufacturers. These tables offer comprehensive data that helps in calculating the maximum loads a particular grating can support. Expertise in interpreting these tables allows for a more accurate selection based on uniform load and concentrated load conditions. For instance, a 1 x 3/16 bar might suffice for pedestrian traffic, but increased thickness would be required for vehicular loads.
bar grating dimensions
When it comes to materials, the choice between carbon steel, stainless steel, and aluminum affects the dimensions as well. Carbon steel bar gratings are robust and cost-effective, making them ideal for heavy-duty applications. In contrast, stainless steel gratings offer excellent resistance to corrosion, a crucial factor for environments exposed to moisture or chemicals. Aluminum gratings, on the other hand, provide a lightweight alternative and are often used where both strength and weight reduction are paramount.
Authoritative insights suggest that industry standards such as those set by the American National Standards Institute (ANSI) and the National Association of Architectural Metal Manufacturers (NAAMM) offer guidelines on bar grating dimensions. Familiarity with these standards ensures compliance and performance consistency across various projects. Trustworthiness is further enhanced when selecting suppliers with certifications and a proven track record of delivering quality materials.
Customization of bar grating dimensions is a common requirement as not every application fits the standard mold. Bespoke solutions often involve precise measurements to accommodate unique architectural designs or specific functional needs. Cutting techniques and finishes also play a substantial role, as serrated grating, for example, is specially crafted to provide additional grip for slip-resistant surfaces, a feature particularly appreciated in oil rigs or maritime environments.
In conclusion, the choice and understanding of bar grating dimensions is not a trivial task. It demands a blend of comprehensive insight into material properties, load requirements, regulatory guidelines, and practical installation concerns. Specialists with extensive background and involvement in projects involving bar grating installations offer valuable guidance to ensure that the chosen gratings not only meet the functional and safety requirements but also offer long-term durability and reliability. Emphasizing experience, expertise, authority, and trustworthiness provides confidence in selecting the appropriate bar grating dimensions for any industrial or commercial project.