Aluminum bar grating is a versatile, durable, and cost-effective material used in various industries for applications ranging from walkways to ventilation covers. One crucial factor when considering aluminum bar grating is its weight, as it directly affects installation, cost, and structural support requirements.
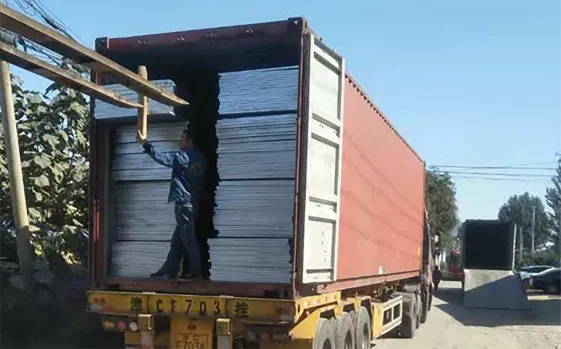
When compared to other metals, such as steel, aluminum is notably lighter, making it easier to handle and install. This lightweight property is particularly advantageous in projects where reducing total load is imperative, such as on rooftops or in mobile platforms. The reduced weight does not compromise durability; aluminum bar grating is resistant to corrosion and retains its strength over time, even in harsh environmental conditions.
From an expertise perspective, aluminum bar grating is offered in various configurations and sizes, further influencing its weight. Typically, it's essential to understand that the weight per square foot will vary depending on parameters like bearing bar thickness, spacing, and the grating pattern (plain, serrated, or I-bar). For instance, a plain rectangular pattern will weigh differently from a serrated pattern intended for high-traction environments.
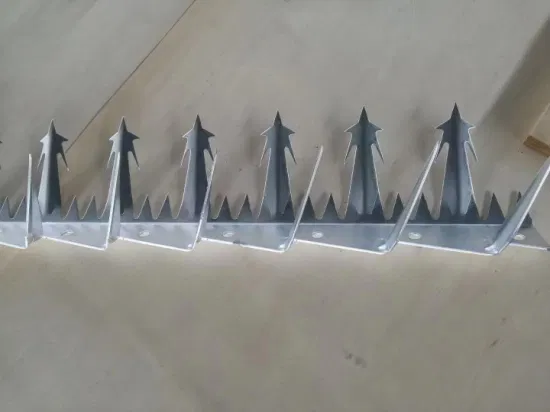
Professionals in the field rely on standards set by organizations such as the National Association of Architectural Metal Manufacturers (NAAMM) to determine the weight and load-bearing capacity of aluminum bar grating. These standards promote safety and reliability across applications by providing guidelines based on rigorous testing and engineering calculations.
The light weight of aluminum bar grating translates to significant advantages in transportation and installation. It requires less manpower and machinery, leading to reduced labor costs and quicker installation times. Moreover, its corrosion resistance eliminates the need for regular maintenance, lowering the long-term operational costs and adding to the overall value of using aluminum over other materials.
aluminum bar grating weight
Experts recommend choosing aluminum bar grating for environments prone to corrosion agents, such as coastal areas or chemical facilities, due to its oxide layer that protects against rust and degradation. It's also superior to steel in terms of electrical and thermal conductivity, making it suitable in applications that require heat or electricity management.
One real-world example of aluminum bar grating's application is in offshore oil rigs, where its lightweight yet sturdy nature enhances the safety and efficiency of installation. Additionally, the natural non-magnetic property of aluminum is essential in environments where magnetic interference must be mitigated, such as in certain scientific or military applications.
Despite its benefits, professionals caution that aluminum may not always be the best choice if extremely high-load capacities are required. In such cases, a hybrid design employing both aluminum for weight reduction and reinforced steel for strength can offer an optimal solution. This flexibility in design and implementation showcases aluminum bar grating's adaptability across a multitude of scenarios.
Trust in using aluminum bar grating is further reinforced through case studies where long-term usage has proven its efficacy in reducing costs while maintaining high performance standards. As industries strive towards more sustainable and lightweight construction materials, aluminum's recyclability adds an environmentally friendly aspect valued by modern businesses.
In summary, understanding the weight implications of aluminum bar grating is essential for making informed decisions about materials in construction and engineering projects. With its multitude of advantages including ease of handling, corrosion resistance, and cost-effectiveness, aluminum continues to be a preferred choice among experts and trusted by professionals worldwide for its performance in demanding environments.