The architectural and industrial sectors have consistently leaned towards products and materials that promise resilience, adaptability, and performance efficiency. Among these, gratings have gained significant prominence for their utility and multifunctionality in various applications, ranging from walkways and platforms to drainage covers and stair treads.
The 19w4 grating is one particular configuration that stands out due to its distinct dimensions and the advantages it brings to the table.
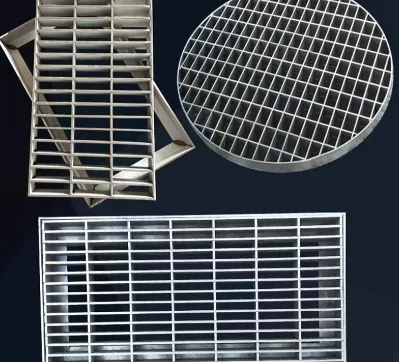
The 19w4 grating, a term familiar to industry connoisseurs, refers to a specific bar grating with a particular setup that meets both aesthetic and functional demands. When it comes to bar gratings, the 19w4 designation precisely points to the spacing and configuration of the bars, which include bearing bars with a spacing of 1-3/16 inches center-to-center and cross bars spaced 4 inches center-to-center. This configuration is meticulously constructed, bearing in mind both the load distribution and visual appeal, ensuring it can support substantial dynamic and static forces while maintaining structural integrity.
From an expertise perspective, the selection of 19w4 grating dimensions suits scenarios demanding considerable load-bearing capacity without a compromise on drainage and light passage. These gratings are predominantly fabricated using carbon steel, aluminum, or stainless steel, each offering distinctive characteristics. Carbon steel gratings are often preferred for their cost-effectiveness and robustness, making them ideal for heavy traffic areas. On the other hand, aluminum gratings are lightweight and offer excellent corrosion resistance, hence their popularity in areas where environmental factors might cause degradation. Stainless steel gratings, though pricier, are indispensable in settings that demand rigorous sanitary conditions, such as food processing facilities or pharmaceutical plants.
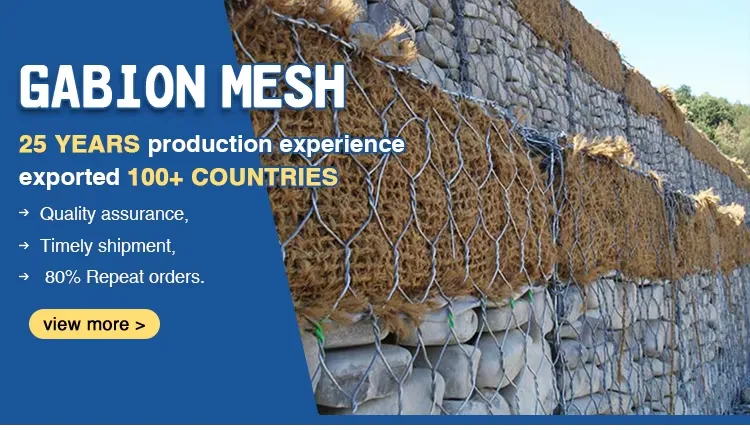
The implementation of 19w4 gratings across various projects underscores its reliability and flexibility. In industrial plants, these gratings provide safe walking surfaces and facilitate effective drainage, reducing the risk of slip, trip, and fall accidents. With an adeptness for customization, 19w4 gratings can be tailored to specific width and length requirements, enhancing their applicability in unique structural designs.
19w4 grating dimensions
Emphasizing robust expertise, the production process of 19w4 gratings involves precise welding techniques that ensure cross bar and bearing bar continuity and strength. This contributes not only to its durability but also enhances the lifespan of the grating, reducing the need for frequent replacements. Moreover, with technological advancements, modern manufacturing processes have resulted in gratings with improved load ratings and better resistance to environmental stressors.
An authoritative standpoint also highlights the consideration of safety standards and compliance with regional and international building codes. Manufacturers producing 19w4 gratings are often compliant with regulations such as the Occupational Safety and Health Administration (OSHA) standards in the United States, underscoring their commitment to providing high-quality, safe products for industries and businesses.
The trustworthiness of 19w4 gratings is further reinforced by testimonials and documented case studies showcasing their performance in demanding environments. For instance, in oil rigs, where conditions are harsh and the demand for durability is high, 19w4 gratings have been lauded for their capacity to withstand pressure while offering minimal maintenance.
To sum up, the 19w4 grating dimensions embody a harmonious blend of expert engineering, authoritative manufacturing processes, and a commitment to safety and reliability, making them a staple in the domain of industrial and commercial applications. For any entity considering the integration of these gratings into their projects, the assurance of quality and performance makes them a prudent choice for both immediate needs and future adaptability.