When it comes to selecting materials for industrial flooring or decking, SS grating stands out as a highly efficient choice due to its robustness and versatility. SS grating, short for stainless steel grating, is particularly favored in environments that demand uncompromised durability and resistance to corrosive elements. With fluctuating market demands and various factors influencing material costs, understanding the pricing dynamics of SS grating becomes crucial for project managers and procurement specialists.
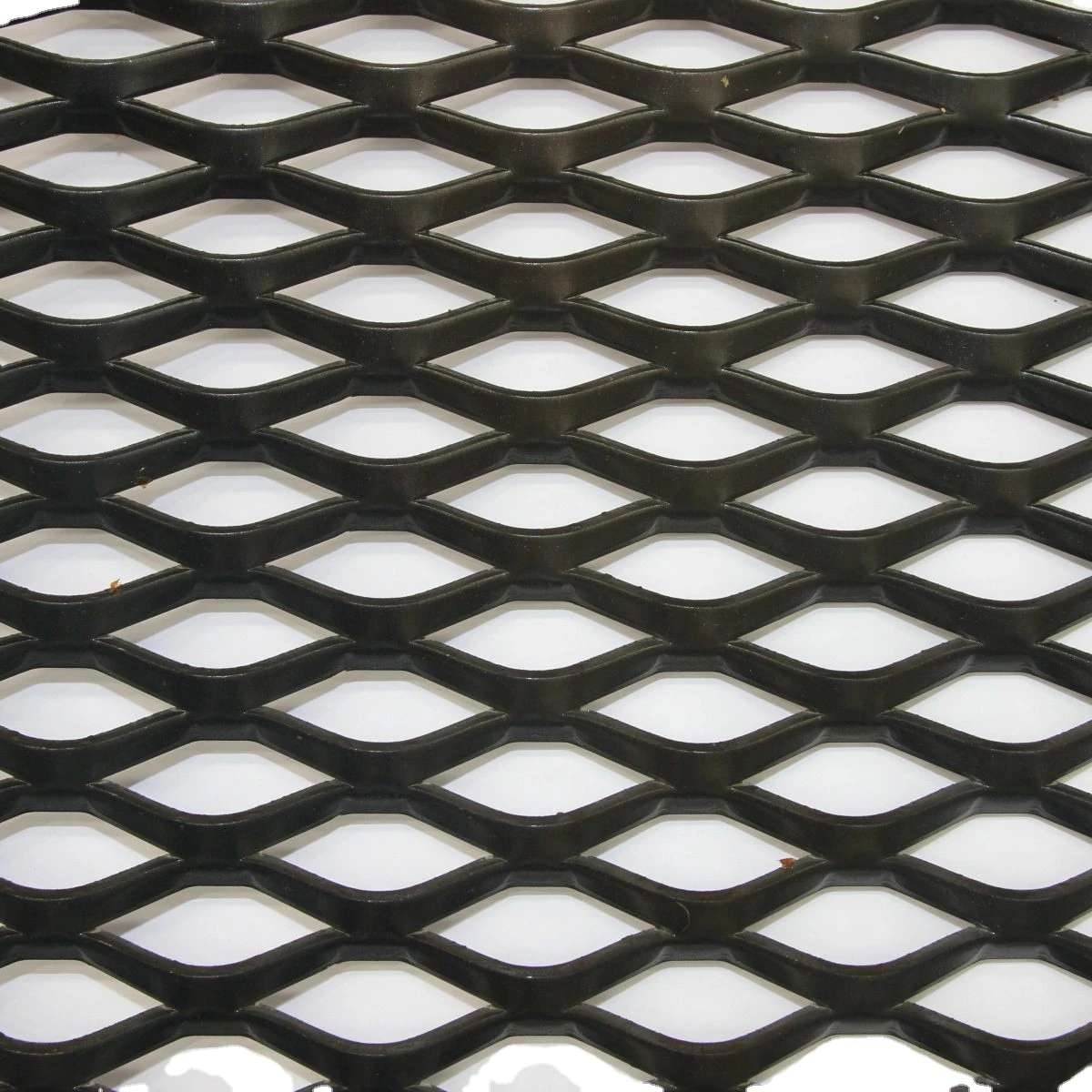
In the industrial sector, the price of SS grating can be affected by multiple variables. Material quality is paramount; stainless steel comes in various grades, such as 304 and 316, each offering distinct levels of corrosion resistance and mechanical strength. Grade 316 is often more expensive due to its superior anti-corrosive properties, making it ideal for maritime or chemical processing environments. It's important to assess the specific requirements of your project to determine the most cost-effective grade without compromising on safety and longevity.
The manufacturing process also plays a significant role in pricing. SS grating can be fabricated using different methods—such as press-locked, welded, or swage-locked—each catering to unique structural needs and cost considerations. Welded grating typically provides the highest strength due to its one-piece construction, making it pricier but indispensable for high-load applications. On the other hand, press-locked grating might offer a cost-saving alternative for applications where maximum load-bearing is not as critical.
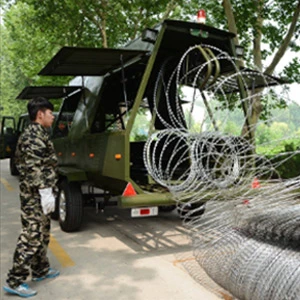
Supply chain dynamics are another influential factor in the pricing of SS grating. Global economic conditions, trade policies, and even geopolitical tensions can cause fluctuations in the availability and cost of raw materials. Recently, issues such as supply chain disruptions and tariffs have influenced the cost of stainless steel globally, subsequently affecting the prices of SS grating. Maintaining awareness of these factors can aid in better budgeting and procurement strategies.
ss grating price
Moreover, customization and additional treatment processes contribute to cost variations. Custom-fabricated gratings to fit unique designs or non-standard dimensions often entail higher expenses. Enhanced treatments, such as galvanization or a specific finish to improve anti-slip properties, can add to the final price but also enhance the grating's suitability for specific environments, thereby adding value through longevity and reduced maintenance costs.
Volume purchasing can also serve as a strategic approach to cost management. Large-scale orders typically drive down the unit price of SS grating due to economies of scale. Organizations with ongoing or multiple projects might consider consolidating their purchases to leverage better pricing from manufacturers or suppliers.
Expounding from real-world experience, a reliable supplier relationship is invaluable. Trusted suppliers offer not only competitive pricing but also essential technical insights, such as the appropriate selection of grades and designs to fit specific applications. They can also provide installation expertise, further safeguarding the investment through a reduction in potential installation errors and associated costs.
In conclusion, navigating the pricing landscape of SS grating involves a dynamic interplay of material selection, manufacturing choices, and strategic purchasing. A comprehensive understanding of these aspects not only ensures cost efficiency but also aligns with the core tenets of Expertise, Authoritativeness, and Trustworthiness—essential for making informed, reliable procurement decisions. Projects that expertly balance these elements can expect optimal performance and longevity from their SS grating installations, ultimately leading to a sound investment and enhanced project outcomes.