When considering the cost of galvanized bar grating, several key factors need to be addressed to understand its value and application. Galvanized bar grating is a vital product used in various industries due to its durability, strength, and the protective zinc coating that guards against corrosion. This comprehensive guide delves into the intricate aspects influencing the cost of galvanized bar grating, drawing from real-world experience and expert insights, ensuring a complete understanding of its pricing dynamics.
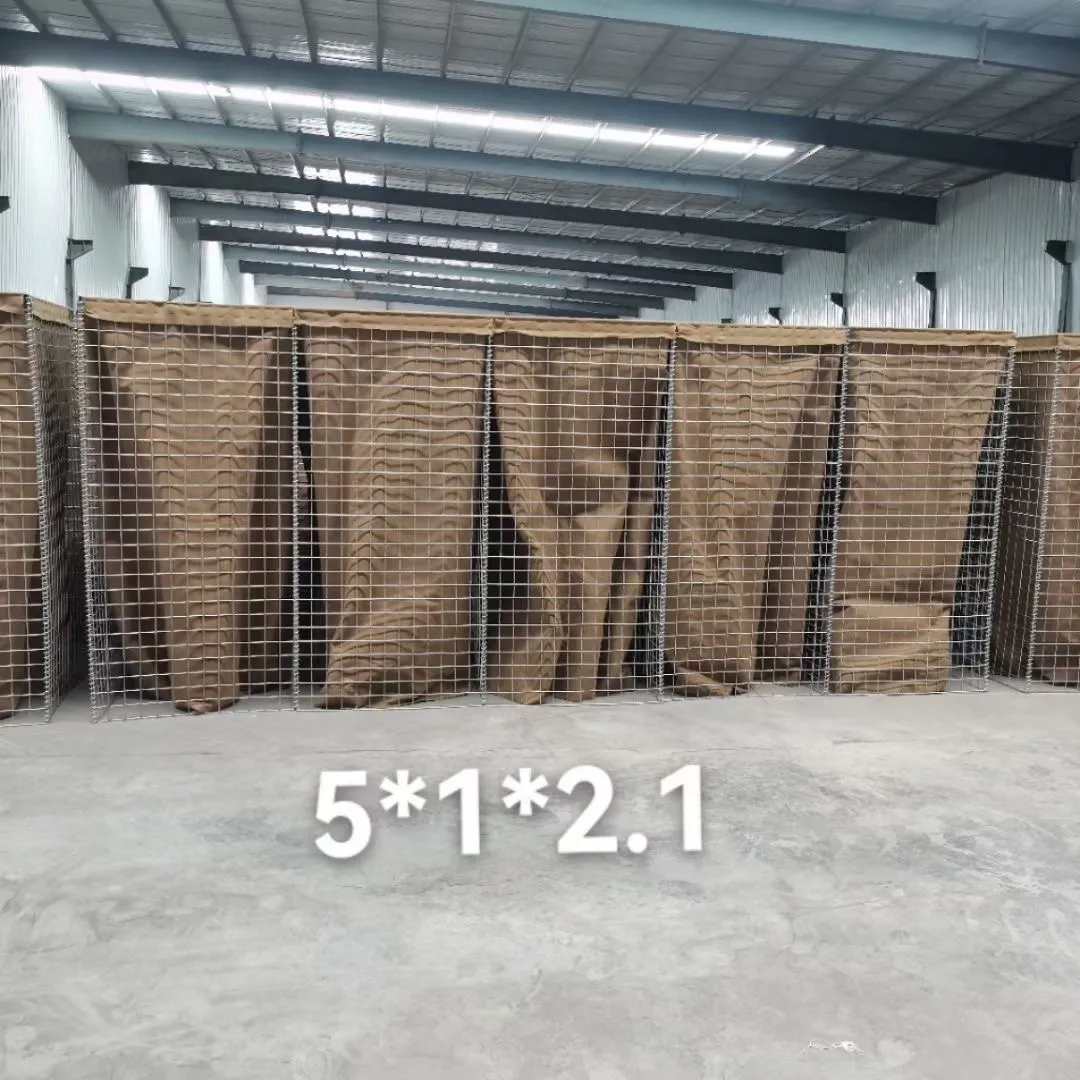
Galvanized bar grating stands out, primarily because of its protective properties and versatile usage. It's frequently employed in industrial flooring, walkways, and safety barriers, where slip resistance and load-bearing capabilities are essential. The galvanization process involves coating the grating with a layer of zinc, providing a robust shield against rust and decay, especially beneficial in harsh environments like offshore platforms or chemical plants.
The initial cost of galvanized bar grating is determined by several components. Material choice is paramount, with steel and aluminum being popular options; each brings its unique strength and weight characteristics. Steel is often preferred for heavy-duty applications due to its superior strength, while aluminum offers a lighter alternative ideal for less demanding environments. This choice significantly impacts the price, with steel generally being more cost-effective but requiring consideration for the additional weight it brings to the application.
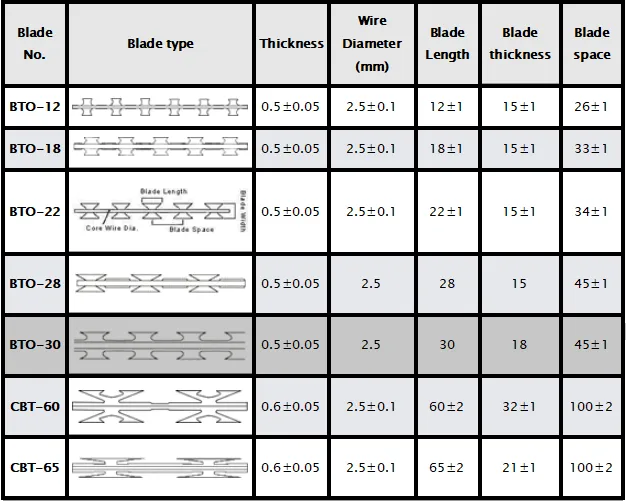
Galvanization is another critical cost factor. The process not only adds to longevity but also peace of mind regarding maintenance and replacement costs due to the grating’s enhanced durability. The thickness of the zinc coating can vary and directly affect pricing, with a thicker coating offering longer corrosion resistance at a higher upfront cost.
Size and design specifications also sway the final price of the grating. Customized sizes or intricate patterns necessitate specialized manufacturing processes, subsequently increasing production expenses. Conversely, standard sizes and designs benefit from economies of scale, leading to more competitive pricing. Industries should evaluate their specific needs to balance cost with functionality, ensuring the grating meets safety and operational requirements without unnecessary expenditure.
galvanized bar grating cost
Installation costs must be factored into the overall expense of galvanized bar grating. While the grating itself might represent a significant portion of the investment, the complexity of installation can add unforeseen costs if not carefully planned. Expert installation can optimize life span and safety, making the initial cost worthwhile over the long-term use.
Transportation also impacts the cost of galvanized bar grating. Due to its consequent weight and volume, the logistics of delivering the material from manufacturer to site can influence total budget considerations. Proximity to suppliers and the choice of transportation mode are pivotal in managing these expenses efficiently.
Finally, market conditions, including supply and demand dynamics and the price of raw materials such as steel, can lead to fluctuations in grating costs. Keeping abreast of these economic factors is crucial for companies looking to make informed purchasing decisions and optimize their investment.
In summary, the cost of galvanized bar grating is influenced by a confluence of factors, including material choice, galvanization thickness, size and customization, installation expenses, and transportation. The strategic balance of these facets ensures not only an optimal cost-benefit ratio but also that safety and durability standards are met or exceeded. By understanding these elements, stakeholders can make knowledgeable decisions, resulting in effective and economical use of galvanized bar grating across industries.