Grating, particularly in industrial and commercial spaces, plays a critical role in ensuring safety, efficiency, and durability. Among the various types, galvanized iron (GI) grating stands out for its strength and corrosion resistance, making it a staple choice across different sectors. Understanding the standard sizes of GI grating is essential for selecting the right fit for your specific needs, ensuring both functionality and cost-effectiveness.
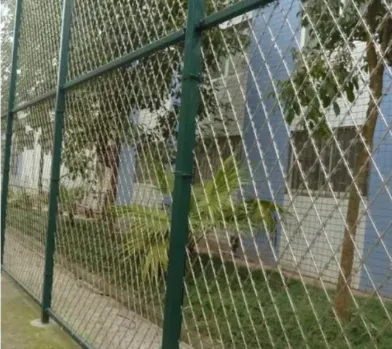
The standard sizes of GI grating are influenced by a range of factors, including load levels, span requirements, and the specific application environment. Typically,
GI grating panels are available in sizes ranging from 1m x 3m to 1.2m x 4m, with variations to accommodate different project specifications. The mesh size – the distance between bearing bars – further dictates how these gratings can be employed effectively. Common mesh sizes include 30mm x 100mm, 30mm x 50mm, and 40mm x 100mm, amongst others.
One of the primary considerations in determining the appropriate GI grating size is the load-bearing capacity required for the installation. Heavier loads will necessitate thicker and denser grating, often with smaller mesh openings, to distribute weight evenly and prevent structural failures. For industries like manufacturing or ports, where equipment and vehicles impose substantial stress, carefully selecting the correct grating size ensures longevity and operational safety.
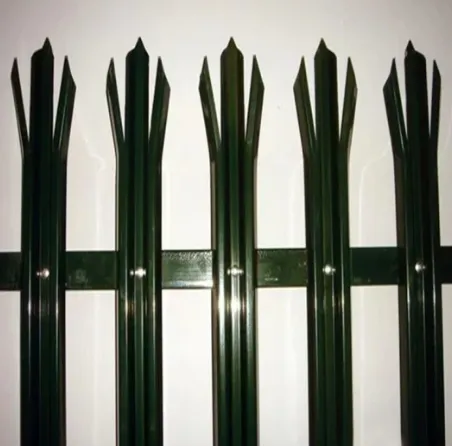
Moreover, the environment in which the grating will be installed can significantly influence sizing decisions. In corrosive environments or those exposed to harsh weather, the protective zinc coating of GI grating offers long-lasting protection against rust and deterioration, but the right size must be chosen to maximize these benefits. Engineers and procurement specialists often rely on standardized manufacturing guidelines to align grating size with environmental demands, ensuring not only the longevity of the installation but also adherence to industry safety standards.
gi grating standard size
From maintenance walkways in power plants to drainage covers in commercial spaces, GI grating plays versatile roles. The customization available in standard sizes allows for installation efficiency and cost-saving measures by minimizing waste and ensuring quick assembly. This adaptability makes standard size knowledge crucial for architects and project managers who aim to optimize space, cost, and project timelines.
For any project, consulting with grating experts provides invaluable insight into the selection process, helping to navigate the myriad of choices and to customize further when necessary. Getting the size right is not merely about filling a space; it's a strategic decision that impacts safety, cost, and project success. As technology advances, the integration of predictive analytics in the construction phase further refines grating size decisions, preemptively addressing potential load and environmental variables.
In summary, GI grating standard sizes are foundational elements in multiple industries, providing the necessary framework to support various activities while ensuring safety and performance. Properly determining and implementing the right grating size aligns with best practices in engineering and construction, offering a balance of durability, safety, and economic feasibility. Emphasizing professional expertise and authority in grating selection reinforces trust and ensures the optimal outcome for any project.